Turbine blades that reduce cooling degradation by regulating the location of internal dust deposits
A technology for turbine blades and cooling effects, which is applied in the direction of supporting components of blades, machines/engines, mechanical equipment, etc., which can solve the problems of affecting the heat transfer capacity and cooling effect of blades, not inhibiting internal dust deposition, and weakening the effect of impact cooling, etc. , to achieve the effects of slowing down the cooling effect, smooth outflow, and ensuring heat exchange capacity
- Summary
- Abstract
- Description
- Claims
- Application Information
AI Technical Summary
Problems solved by technology
Method used
Image
Examples
Embodiment 1
[0029] The turbine blade that slows down the degradation of the cooling effect by adjusting the internal dust deposition position, the turbine blade is a double-wall structure, specifically including the inner wall 1, the outer wall 2 and the spoiler column 3, the spoiler column 3 is located between the inner wall 1 and the outer wall 2, and the outer wall 2 The air film hole 4 is arranged on the inner wall 1, the jet hole 5 is arranged on the inner wall 1, and the shielding structure 6 is connected on the inner wall 1, and the shielding structure 6 is located upstream of the jet hole 5, such as figure 2 , image 3 and Figure 7 shown;
[0030] The height of inner wall 1 is 1mm, the diameter of jet hole 5 is 1mm, the height of outer wall 2 is 1mm, the distance between inner wall 1 and outer wall 2 is 1mm; the diameter of air film hole 4 is 0.4mm, the horizontal distance between the center of air film hole 4 and the center of jet hole 5 is 8mm, and the vertical distance 8mm;...
Embodiment 2
[0033] The turbine blade that slows down the degradation of the cooling effect by adjusting the internal dust deposition position, the turbine blade is a double-wall structure, specifically including the inner wall 1, the outer wall 2 and the spoiler column 3, the spoiler column 3 is located between the inner wall 1 and the outer wall 2, and the outer wall 2 The air film hole 4 is arranged on the inner wall 1, the jet hole 5 is arranged on the inner wall 1, and the shielding structure 6 is connected on the inner wall 1, and the shielding structure 6 is located upstream of the jet hole 5, such as Figure 4 and Figure 7 shown;
[0034] The height of inner wall 1 is 1mm, the diameter of jet hole 5 is 1mm, the height of outer wall 2 is 1mm, the distance between inner wall 1 and outer wall 2 is 1mm; the diameter of air film hole 4 is 0.4mm, the horizontal distance between the center of air film hole 4 and the center of jet hole 5 is 8mm, and the vertical distance 8mm; the diamete...
Embodiment 3
[0037] The turbine blade that slows down the degradation of the cooling effect by adjusting the internal dust deposition position, the turbine blade is a double-wall structure, specifically including the inner wall 1, the outer wall 2 and the spoiler column 3, the spoiler column 3 is located between the inner wall 1 and the outer wall 2, and the outer wall 2 The air film hole 4 is arranged on the inner wall 1, the jet hole 5 is arranged on the inner wall 1, and the shielding structure 6 is connected on the inner wall 1, and the shielding structure 6 is located upstream of the jet hole 5, such as Figure 5 and Figure 7 shown;
[0038] The height of inner wall 1 is 1mm, the diameter of jet hole 5 is 1mm, the height of outer wall 2 is 1mm, the distance between inner wall 1 and outer wall 2 is 1mm, and the diameter of air film hole 4 is 0.4mm; the horizontal distance between the center of air film hole 4 and the center of jet hole 5 is 8mm, and the vertical distance 8mm; the dia...
PUM
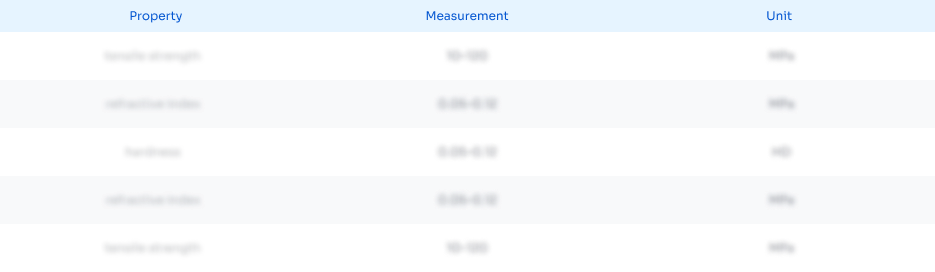
Abstract
Description
Claims
Application Information

- R&D
- Intellectual Property
- Life Sciences
- Materials
- Tech Scout
- Unparalleled Data Quality
- Higher Quality Content
- 60% Fewer Hallucinations
Browse by: Latest US Patents, China's latest patents, Technical Efficacy Thesaurus, Application Domain, Technology Topic, Popular Technical Reports.
© 2025 PatSnap. All rights reserved.Legal|Privacy policy|Modern Slavery Act Transparency Statement|Sitemap|About US| Contact US: help@patsnap.com