Concrete prefabricated part laminated plate production die parts and manufacturing method as well as concrete prefabricated part laminated plate production die
A technology of prefabricated components and laminated panels, applied in the direction of molds, etc., to achieve the effects of easy cleaning, less pollution, and easy demolition
- Summary
- Abstract
- Description
- Claims
- Application Information
AI Technical Summary
Problems solved by technology
Method used
Image
Examples
Embodiment Construction
[0042] The present invention will be described in detail below in conjunction with specific embodiments and accompanying drawings.
[0043] as attached Figure 1-15 As shown, a production mold for composite slabs of prefabricated concrete components includes bottom formwork 1, side mold fixed magnetic box 2, mold pressure plate 3, threaded steel mesh sheet 4, end mold closed-hole sealing self-adhesive strip 5, and lower mold end mold aluminum profile 6. Upper mold end mold aluminum profile 7, end mold baffle plate 8, lower mold side mold aluminum profile 9, upper mold side mold aluminum profile 10, side mold closed hole sealing self-adhesive strip 11, bottom mold positioning block 12, lower mold Side mold aluminum profile connector 13, upper mold side mold aluminum profile connector 14, lower mold end mold aluminum profile connector 15, upper mold end mold aluminum profile connector 16, plastic sheet 17, self-adhesive protective film 18, self-adhesive Adhesive 19, closed-cell...
PUM
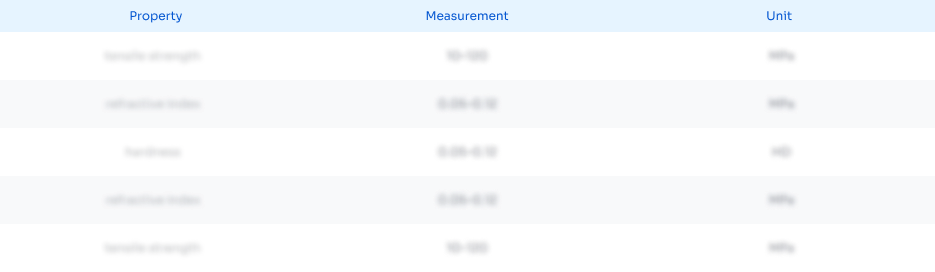
Abstract
Description
Claims
Application Information

- R&D
- Intellectual Property
- Life Sciences
- Materials
- Tech Scout
- Unparalleled Data Quality
- Higher Quality Content
- 60% Fewer Hallucinations
Browse by: Latest US Patents, China's latest patents, Technical Efficacy Thesaurus, Application Domain, Technology Topic, Popular Technical Reports.
© 2025 PatSnap. All rights reserved.Legal|Privacy policy|Modern Slavery Act Transparency Statement|Sitemap|About US| Contact US: help@patsnap.com