Thin film insulating core non-conducting electrode cap and annular nugget resistance spot welding method
A conductive electrode and electrode cap technology, applied in resistance welding equipment, electrode features, welding equipment, etc., can solve the problems of reducing the shear strength and corrosion resistance of the joint, overheating and large deformation of the joint, and achieve good cooling and heat dissipation performance. , Reduce the penetration rate and solve the effect of deep indentation
- Summary
- Abstract
- Description
- Claims
- Application Information
AI Technical Summary
Problems solved by technology
Method used
Image
Examples
Embodiment Construction
[0035] The detailed content of the present invention and its specific implementation will be further described below in conjunction with the accompanying drawings.
[0036] see Figure 1 to Figure 3 As shown, the film insulation core non-conductive electrode cap and the ring-shaped nugget resistance spot welding method of the present invention aim to reduce the indentation depth of the spot welding joint and the deformation of the workpiece, and further improve the joint performance of the resistance spot welding. The non-conductive electrode cap with film insulation core is mainly composed of two parts, namely the core part of the electrode cap and the peripheral part. Both parts are homogeneous materials with good thermal conductivity, and the heat dissipation effect is the same as that of traditional electrode caps. The outer surface of the core is sprayed with a layer of thin film insulating material to achieve the insulating effect. The core with a thin film insulating l...
PUM
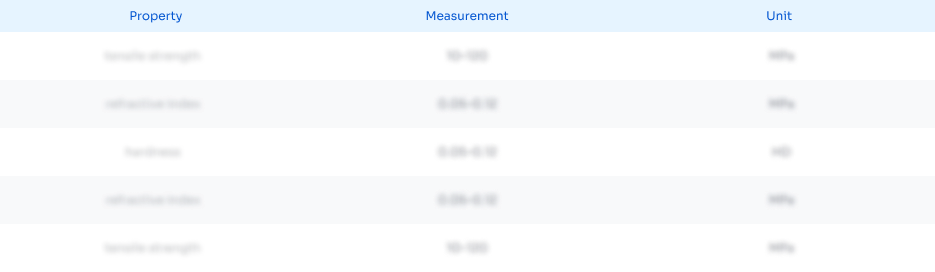
Abstract
Description
Claims
Application Information

- R&D
- Intellectual Property
- Life Sciences
- Materials
- Tech Scout
- Unparalleled Data Quality
- Higher Quality Content
- 60% Fewer Hallucinations
Browse by: Latest US Patents, China's latest patents, Technical Efficacy Thesaurus, Application Domain, Technology Topic, Popular Technical Reports.
© 2025 PatSnap. All rights reserved.Legal|Privacy policy|Modern Slavery Act Transparency Statement|Sitemap|About US| Contact US: help@patsnap.com