Method for predicting and optimizing abrasion of valve in pneumatic conveying system
A technology of a pneumatic conveying system and an optimization method, applied in the field of valves, can solve the problems of high gas velocity, particle erosion and wear, consuming a lot of manpower, material and financial resources, etc.
- Summary
- Abstract
- Description
- Claims
- Application Information
AI Technical Summary
Problems solved by technology
Method used
Image
Examples
Embodiment Construction
[0062] Below in conjunction with the accompanying drawings, the present invention will be further described by taking a ball valve as an example.
[0063] Embodiments of the present invention and its implementation process are as follows:
[0064] Step 1: Obtain the ball valve pipeline model
[0065] 1. Establish a ball valve model
[0066] According to the actual structure in engineering application, the pipe diameter at the valve is D, use SolidWorks software or other 3D modeling software to carry out 3D modeling of the ball valve on the pipeline to obtain the 3D model of the ball valve;
[0067] 2. Establish the pipeline structure at the ball valve
[0068] Extend the upstream pipeline of the ball valve in the 3D model by 30D; extend the downstream pipeline to 20D to obtain the pipeline structure of the ball valve, such as image 3 shown;
[0069] 3. Simplify the structure
[0070] According to the function and characteristics of the ball valve, the structure of the ba...
PUM
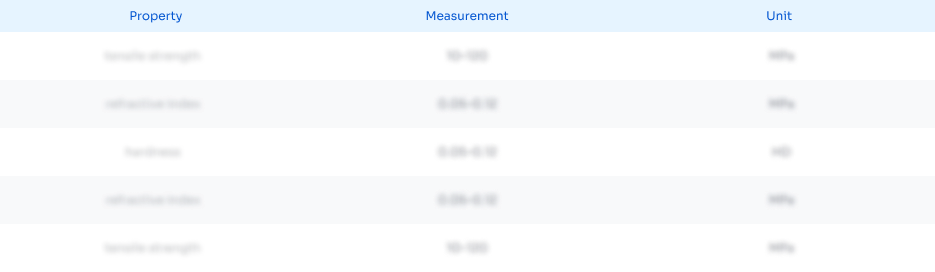
Abstract
Description
Claims
Application Information

- R&D Engineer
- R&D Manager
- IP Professional
- Industry Leading Data Capabilities
- Powerful AI technology
- Patent DNA Extraction
Browse by: Latest US Patents, China's latest patents, Technical Efficacy Thesaurus, Application Domain, Technology Topic, Popular Technical Reports.
© 2024 PatSnap. All rights reserved.Legal|Privacy policy|Modern Slavery Act Transparency Statement|Sitemap|About US| Contact US: help@patsnap.com