Heat flow control system and method for thermal environment simulation test of attitude control power system
A thermal environment simulation and power system technology, applied in space navigation conditions simulation devices, space navigation equipment, transportation and packaging, etc., can solve the lack of continuity and reliability of heat flux control of lamp arrays, lack of early warning and emergency treatment, etc. question
- Summary
- Abstract
- Description
- Claims
- Application Information
AI Technical Summary
Problems solved by technology
Method used
Image
Examples
Embodiment 1
[0055] Embodiment 1: Closed-loop control method
[0056] Such as figure 1 As shown, the specific method of closed-loop control is as follows:
[0057] 1) Set the proportional, integral and differential control parameters under different target heat flow values; establish the corresponding relationship of membership function and control rules corresponding to different target heat flow values; make the corresponding relationship table between heat flow value and control parameters;
[0058] 2) According to the required heat flux curve, by means of interpolation, the corresponding heat flow value is obtained at intervals of one second, and the corresponding relationship table between time and heat flow value is made.
[0059] During the test, the heat flow value of the heat flow meter is collected by the temperature controller; the upper computer reads the heat flow value collected by the temperature controller in LAN mode, and obtains the corresponding target heat flow value a...
Embodiment 2
[0068] Embodiment 2, open-loop control method
[0069] Such as figure 2 As shown, the specific method of open-loop control is as follows:
[0070] 1) According to the required heat flux curve, by means of interpolation, the corresponding heat flow value is obtained at intervals of 5 seconds, and the corresponding relationship table between time and heat flow value is made. Wherein the time interval of the closed-loop control interpolation in embodiment 1 is 1s, the time interval of the interpolation of the open-loop control in embodiment 2 is 5s, and the timeliness of closed-loop control is stronger, therefore can set the time interval smaller, the higher precision time interval.
[0071] 2) Complete the open-loop calibration work, and calibrate different heat flow values and output voltage values of the thyristor power output device according to the corresponding relationship table between time and heat flow value. After the calibration is completed, the obtained data...
Embodiment 3
[0079] Embodiment 3, closed-loop and open-loop control
[0080] In order to prevent the closed-loop heat flow meter from being damaged or the measurement accuracy being greatly disturbed by the outside world during the test, the heat flow control program has the ability to quickly switch the thermal environment simulation system from closed-loop control to open-loop control. When switching to open-loop control, open The execution time of the loop control program is consistent with the execution time of the closed-loop control program, so as to ensure the program integrity of the test process.
[0081] In the process of closed-loop and open-loop control, the voltage curves of each partition of the thermal environment device are collected and displayed in real time. When the difference between the voltage value and the predetermined voltage value exceeds the predetermined range, an early warning display is performed for the partition to determine whether to cut in Open loop cont...
PUM
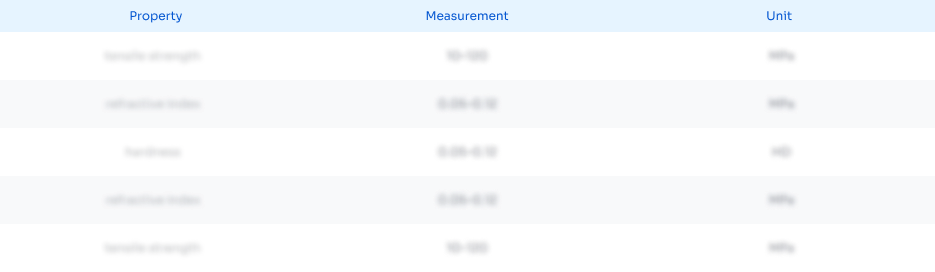
Abstract
Description
Claims
Application Information

- R&D
- Intellectual Property
- Life Sciences
- Materials
- Tech Scout
- Unparalleled Data Quality
- Higher Quality Content
- 60% Fewer Hallucinations
Browse by: Latest US Patents, China's latest patents, Technical Efficacy Thesaurus, Application Domain, Technology Topic, Popular Technical Reports.
© 2025 PatSnap. All rights reserved.Legal|Privacy policy|Modern Slavery Act Transparency Statement|Sitemap|About US| Contact US: help@patsnap.com