Vertical cooling kiln and mineral aggregate cooling and waste heat recovery method
A technology of ore material and cooling air, which is applied in the field of vertical cooling kiln and ore material cooling and waste heat recovery, can solve the problem of the waste heat recovery efficiency that the ore material cannot be uniformly cooled, and achieve the effect of improving waste heat recovery efficiency, efficient recovery and realizing waste heat.
- Summary
- Abstract
- Description
- Claims
- Application Information
AI Technical Summary
Problems solved by technology
Method used
Image
Examples
Embodiment 1
[0039] see Figure 1 to Figure 5 As shown, the present embodiment provides a vertical cooling kiln, comprising:
[0040] The kiln body 101, the bottom of the kiln body 101 is a cooling air supply chamber, the top of the kiln body 101 is a hot air concentration chamber 103, at least one cooling unit cavity is arranged between the cooling air supply chamber and the hot air concentration chamber 103 The cooling unit chamber is used to communicate with the material receiving port of the discharge machine 100; the cooling air supply chamber is used to provide cooling air to the cooling unit chamber, and the hot air concentration chamber 103 is used to communicate with the hot air delivery channel 104 ;
[0041]The inner ring air supply device, the inner ring air inlet 117 of the inner ring air supply device communicates with the cooling air supply chamber, and the inner ring air outlet 118 of the inner ring air supply device communicates with the cooling unit chamber, for making t...
Embodiment 2
[0081] The embodiment of the present invention provides a method for mineral material cooling and waste heat recovery, which is carried out by using the vertical cooling kiln provided by the present invention, wherein the number of cooling unit chambers is one, and the method includes the following steps:
[0082] Fill the cooling unit chamber with mineral material;
[0083] Supply cooling air to the cooling unit chamber;
[0084] Continuous or intermittent discharge of mineral material in the chamber of the cooling unit.
[0085] The embodiment of the present invention also provides a method for mineral material cooling and waste heat recovery, which is carried out by using the vertical cooling kiln provided by the present invention, wherein the number of cooling unit chambers is multiple, and the method includes the following steps:
[0086] Fill the cooling unit chamber with mineral material;
[0087] Supply cooling air to the cooling unit chamber;
[0088] The mineral m...
PUM
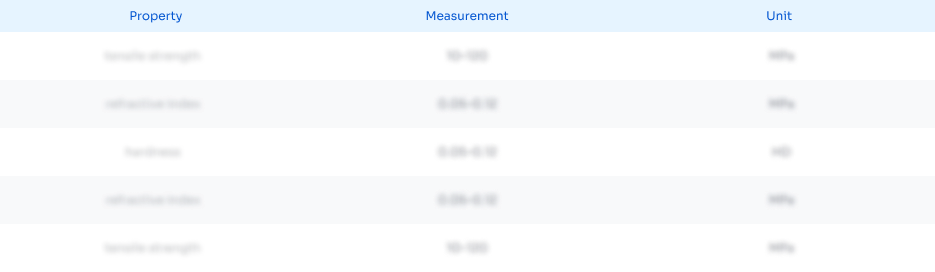
Abstract
Description
Claims
Application Information

- R&D
- Intellectual Property
- Life Sciences
- Materials
- Tech Scout
- Unparalleled Data Quality
- Higher Quality Content
- 60% Fewer Hallucinations
Browse by: Latest US Patents, China's latest patents, Technical Efficacy Thesaurus, Application Domain, Technology Topic, Popular Technical Reports.
© 2025 PatSnap. All rights reserved.Legal|Privacy policy|Modern Slavery Act Transparency Statement|Sitemap|About US| Contact US: help@patsnap.com