High-corrosion-resistance light resin concrete without restrained shrinkage and preparation method thereof
A resin concrete, lightweight technology, used in ceramic products, sustainable waste treatment, solid waste management, etc., can solve problems such as easy cracks, reduce early curing shrinkage, reduce shrinkage, and solve the problem of unstable concrete volume. Effect
- Summary
- Abstract
- Description
- Claims
- Application Information
AI Technical Summary
Problems solved by technology
Method used
Examples
preparation example Construction
[0028] A zero-constraint shrinkage and high corrosion-resistant lightweight resin concrete and a preparation method thereof, comprising the following steps:
[0029] S1: Carry out close packing experiments and theoretical calculations of aggregates to determine the dosage of various aggregates;
[0030] S2: Put the coarse aggregate, sand, fly ash, waste rubber particles and waste rubber powder into the drying box to dry, and after cooling, accurately weigh the coarse aggregate, sand and various fillers, and then stir and mix them evenly;
[0031] S3: Stir the resin, accelerator and curing agent for 2 to 10 minutes, and mix well;
[0032] S4: Pour the mixed aggregates, fillers and chopped fibers into the mixer and continue stirring for 2-8 minutes. After stirring evenly, a lightweight resin concrete with zero constraint shrinkage and high corrosion resistance is prepared.
Embodiment 1
[0035] Resin system 13.0%, lightweight porous coarse aggregate 43.8%, sand 32.9%, fly ash 6.8%, waste rubber particles 2.0%, waste rubber powder 1.2% and chopped fiber 0.3%.
[0036] Preparation method: put lightweight porous coarse aggregate, sand, fly ash, waste rubber particles and waste rubber powder into a drying box to dry, after cooling, accurately weigh the mass of various coarse aggregates and fillers, and then mix and stir Uniformly; then stir the resin, accelerator and curing agent for 5 minutes, and mix well; pour the mixed aggregate, filler and chopped fiber into the mixer and continue to stir for 4 minutes, after stirring evenly, a zero-constraint shrinkage high corrosion resistance lightweight resin concrete.
Embodiment 2
[0038] 14.0% resin system, 42.8% lightweight porous coarse aggregate, 32.9% sand, 6.5% fly ash, 2.0% waste rubber particles, 1.5% waste rubber powder and 0.3% chopped fiber.
[0039] Preparation method: put lightweight porous coarse aggregate, sand, fly ash, waste rubber particles and waste rubber powder into a drying box to dry, after cooling, accurately weigh the mass of various coarse aggregates and fillers, and then mix and stir Uniformly; then stir the resin, accelerator and curing agent for 5 minutes, and mix well; pour the mixed aggregate, filler and chopped fiber into the mixer and continue to stir for 4 minutes, after stirring evenly, a zero-constraint shrinkage high corrosion resistance lightweight resin concrete.
PUM
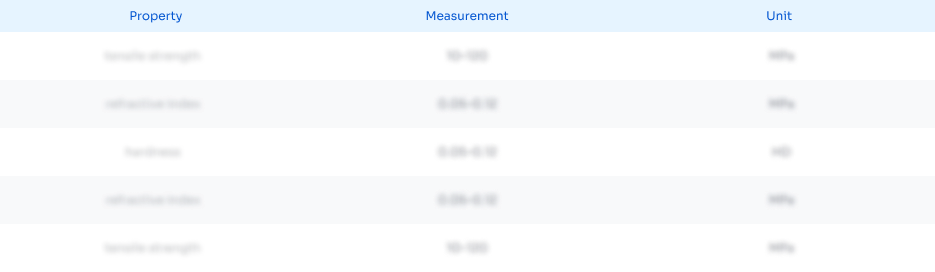
Abstract
Description
Claims
Application Information

- Generate Ideas
- Intellectual Property
- Life Sciences
- Materials
- Tech Scout
- Unparalleled Data Quality
- Higher Quality Content
- 60% Fewer Hallucinations
Browse by: Latest US Patents, China's latest patents, Technical Efficacy Thesaurus, Application Domain, Technology Topic, Popular Technical Reports.
© 2025 PatSnap. All rights reserved.Legal|Privacy policy|Modern Slavery Act Transparency Statement|Sitemap|About US| Contact US: help@patsnap.com