Machining device and method for double-layer casing of aero-engine
A technology for aero-engines and processing devices, applied to aircraft parts, manufacturing tools, transportation and packaging, etc., can solve the problems of increased processing costs, low processing efficiency, and difficulty in realization, and achieve improved processing efficiency, convenient operation, and higher pass rate Effect
- Summary
- Abstract
- Description
- Claims
- Application Information
AI Technical Summary
Problems solved by technology
Method used
Image
Examples
Embodiment Construction
[0033] The technical solution of the present invention will be further described below in conjunction with the accompanying drawings, but the claimed protection scope is not limited to the description.
[0034] Such as Figure 1 ~ Figure 3 As shown, the aero-engine double-layer casing processing device includes an end face gland 1, an outer shell 2, an inner sleeve 3, a movable tension block 4, an air bag 5, a support rod 6, a support arm nut 7, a support arm 8, a connecting seat, a ball Head guide rod 9, inner hole fixed claw 10, outer column 11, transverse plug 12 and pressing plate 13.
[0035] Specifically, the shell 2 includes a cylindrical first shell, the lower end of the first shell is connected to the cylindrical second shell, the first shell is coaxial with the second shell and the outer diameter of the second shell is Greater than the outer diameter of the first casing, the outer diameter of the first casing is slightly smaller than the inner diameter of the double...
PUM
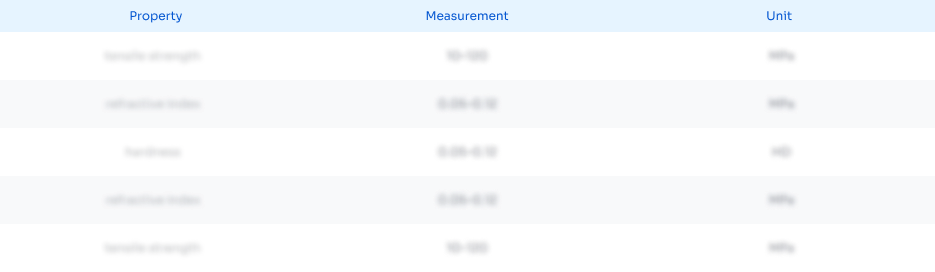
Abstract
Description
Claims
Application Information

- R&D
- Intellectual Property
- Life Sciences
- Materials
- Tech Scout
- Unparalleled Data Quality
- Higher Quality Content
- 60% Fewer Hallucinations
Browse by: Latest US Patents, China's latest patents, Technical Efficacy Thesaurus, Application Domain, Technology Topic, Popular Technical Reports.
© 2025 PatSnap. All rights reserved.Legal|Privacy policy|Modern Slavery Act Transparency Statement|Sitemap|About US| Contact US: help@patsnap.com