Forming conductive vias using a light guide
A technology of light guide and photoresist, which is applied in the formation of electrical connections of printed components, originals for photomechanical processing, optics, etc., which can solve problems such as expensive processes, limiting high-speed PCB density and complexity, etc.
- Summary
- Abstract
- Description
- Claims
- Application Information
AI Technical Summary
Problems solved by technology
Method used
Image
Examples
Embodiment Construction
[0036] The present invention provides a method and structure. In an exemplary embodiment, the method includes: providing a through hole in a base material in a direction perpendicular to a plane of the base material; applying a photoresist layer to an inner surface of the through hole, inserting a light guide into the through hole In the through hole, a portion of the photoresist layer is exposed through the light guide, thereby generating an exposed portion of the photoresist layer and an unexposed portion of the photoresist layer, removing the a portion of the photoresist layer and metal plated the area of the through hole from which the photoresist layer was removed, thereby obtaining the metal plated portion of the through hole and the through hole. The portion of the hole that is not plated with metal.
[0037] In an exemplary embodiment, the method includes providing a via in a base material including at least two copper lines and at least one insulating layer separat...
PUM
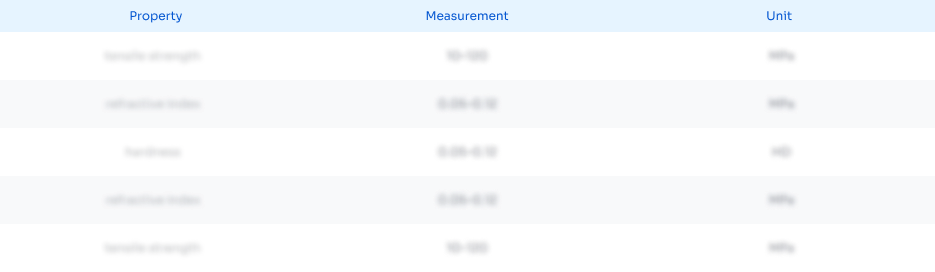
Abstract
Description
Claims
Application Information

- R&D Engineer
- R&D Manager
- IP Professional
- Industry Leading Data Capabilities
- Powerful AI technology
- Patent DNA Extraction
Browse by: Latest US Patents, China's latest patents, Technical Efficacy Thesaurus, Application Domain, Technology Topic, Popular Technical Reports.
© 2024 PatSnap. All rights reserved.Legal|Privacy policy|Modern Slavery Act Transparency Statement|Sitemap|About US| Contact US: help@patsnap.com