Automatic welding method and welding device of ship curved plate
A technology of automatic welding and curved panels, applied in welding equipment, arc welding equipment, manufacturing tools, etc., can solve the problems of carbon planing removal, deviation, welding bead offset, etc., to achieve the effect of improving performance and quality
- Summary
- Abstract
- Description
- Claims
- Application Information
AI Technical Summary
Problems solved by technology
Method used
Image
Examples
Embodiment Construction
[0040] The technical solutions of the present invention will be further described below in conjunction with the accompanying drawings and through specific implementation methods. It should be understood that the specific embodiments described here are only used to explain the present invention, but not to limit the present invention. In addition, it should be noted that, for the convenience of description, only the parts related to the present invention are shown in the drawings but not all of them.
[0041] Some orientation words are limited in the present invention, and under the situation of not making contrary description, the orientation words used are as " upper ", " lower ", " left ", " right ", " inner ", " outer " these orientation words It is adopted for easy understanding, and thus does not constitute a limitation to the protection scope of the present invention.
[0042] In the present invention, unless otherwise clearly specified and limited, a first feature bein...
PUM
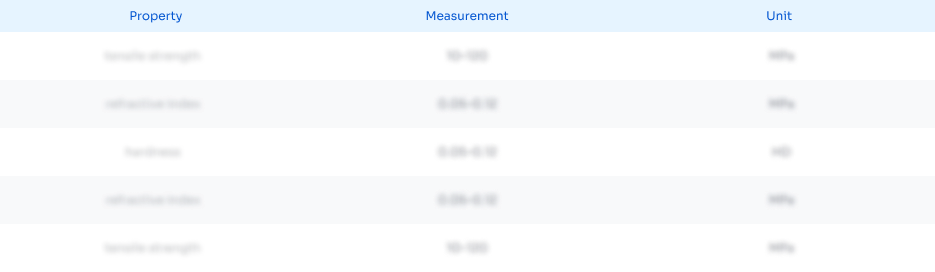
Abstract
Description
Claims
Application Information

- R&D
- Intellectual Property
- Life Sciences
- Materials
- Tech Scout
- Unparalleled Data Quality
- Higher Quality Content
- 60% Fewer Hallucinations
Browse by: Latest US Patents, China's latest patents, Technical Efficacy Thesaurus, Application Domain, Technology Topic, Popular Technical Reports.
© 2025 PatSnap. All rights reserved.Legal|Privacy policy|Modern Slavery Act Transparency Statement|Sitemap|About US| Contact US: help@patsnap.com