A Stiffness Measuring Device of an Electric Actuator
A technology of measuring devices and actuators, which is applied in the servo field, can solve the problems of low rigidity accuracy, achieve high rigidity, and avoid product deformation and displacement errors
- Summary
- Abstract
- Description
- Claims
- Application Information
AI Technical Summary
Problems solved by technology
Method used
Image
Examples
Embodiment Construction
[0043] In order to make the technical solutions and advantages in the embodiments of the present application clearer, the exemplary embodiments of the present application will be further described in detail below in conjunction with the accompanying drawings. Apparently, the described embodiments are only part of the embodiments of the present application, and Not an exhaustive list of all embodiments. It should be noted that, in the case of no conflict, the embodiments in the present application and the features in the embodiments can be combined with each other.
[0044] Such as figure 1 with figure 2 As shown, the embodiment of the present application provides a stiffness measurement device 1 of an electric actuator 13, the stiffness measurement device 1 includes an upper platform body 11, a lower platform body 12, a plurality of parallel electric actuators 13, a hydraulic loading servo system 14 and detection unit (not shown in the figure); Wherein: upper platform body ...
PUM
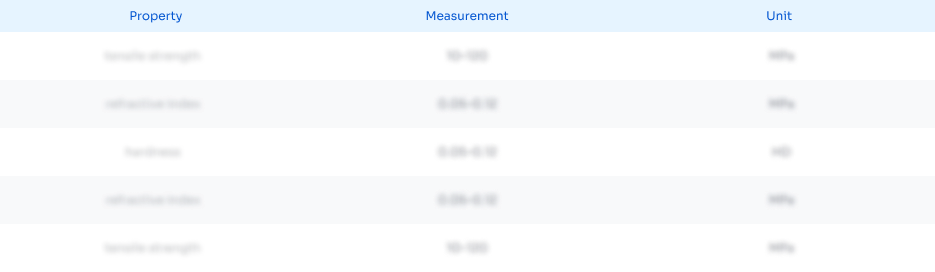
Abstract
Description
Claims
Application Information

- R&D Engineer
- R&D Manager
- IP Professional
- Industry Leading Data Capabilities
- Powerful AI technology
- Patent DNA Extraction
Browse by: Latest US Patents, China's latest patents, Technical Efficacy Thesaurus, Application Domain, Technology Topic, Popular Technical Reports.
© 2024 PatSnap. All rights reserved.Legal|Privacy policy|Modern Slavery Act Transparency Statement|Sitemap|About US| Contact US: help@patsnap.com