A shield machine with robot tool changing function
A technology of robots and shield machines, applied in mining equipment, tunnels, earthwork drilling and mining, etc., can solve the problems of shield machine tool change difficulties, improve tool change efficiency and operational safety factor, and make tool change procedures simple and orderly , the effect of ingenious structural design
- Summary
- Abstract
- Description
- Claims
- Application Information
AI Technical Summary
Problems solved by technology
Method used
Image
Examples
Embodiment 2
[0047] Example 2, such as Figure 4 As shown, a shield machine with robot tool changing function, the end effector 6-1 includes a movement adjustment mechanism 6-1-5, and the movement adjustment mechanism 6-1-5 is provided with a jaw assembly 6-1 -1. Image collection mechanism 6-1-2, bolt tightening mechanism 6-1-4 and high-pressure cleaning mechanism 6-1-3. The image collection mechanism is used to collect images when the end actuator performs actions, which is convenient for visual detection. The bolt tightening mechanism is used for screwing the bolts for installing the cutter; the high-pressure cleaning mechanism 3 is used for cleaning the cutter to be replaced. The jaw assembly 6-1-1, the image acquisition mechanism 6-1-2, the bolt tightening mechanism 6-1-4 and the high pressure cleaning mechanism 6-1-3 are located on the same board surface of the motion adjustment mechanism 6-1-5. The five parts are used together to realize efficient and safe replacement of knives.
...
Embodiment 3
[0053] Example 3, such as Figure 7 As shown, an end effector based on a tool changing robot, the jaw assembly 6-1-1 includes a fixed jaw 101 and a moving jaw 102, the moving jaw 102 is hinged to the fixed jaw 101 and is opened and closed by a clamping cylinder 108 , that is, under the expansion and contraction of the clamping cylinder, the moving claw moves relative to the fixed claw to realize whether the tool is grasped or not. The top of the fixed claw 101 is connected with the sliding drive mechanism. Under the action of the sliding drive mechanism, the fixed claw and the movable claw can slide and translate to realize the change of their positions, so as to adapt to the disassembly and replacement of tools in different positions.
[0054] Further, the sliding drive mechanism includes a guide rail 105, the guide rail 105 is fixed in the connecting box 502, a slider 103 is slid on the guide rail 105, the slider 103 is fixedly connected with the fixed claw 101, and the sli...
Embodiment 4
[0057] Example 4, such as Figure 8 As shown, an end effector based on a tool changing robot, the image acquisition mechanism 6-1-2 includes a camera 201 and a multi-degree-of-freedom adjustment platform 202, and the multi-degree-of-freedom adjustment platform 202 is located in the connection box 502 and extends upward Connect the side of the box body 502 corresponding to the jaw assembly. The camera 201 is arranged on the upper part of the multi-degree-of-freedom adjustment platform 202 through the second rotation mechanism 203. The degree of freedom adjustment platform can drive the camera to swing and lift, and the rotation mechanism drives the camera to rotate, and cooperate with it to realize its own position and angle adjustment. The multi-degree-of-freedom adjustment platform 202 includes a fixed platform 2-1 and a moving platform 2-2, a swing lifting mechanism is arranged between the fixed platform 2-1 and the moving platform 2-2, and the swing lifting mechanism drives...
PUM
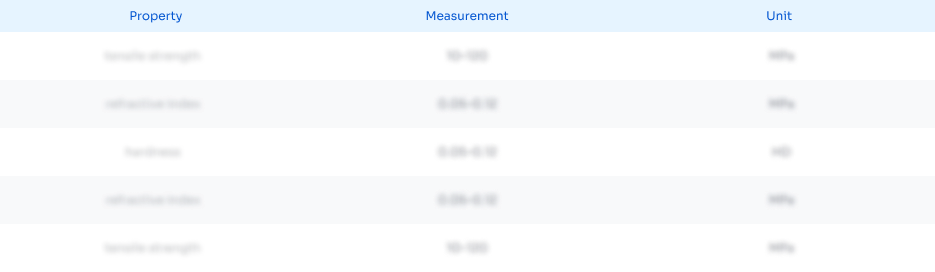
Abstract
Description
Claims
Application Information

- R&D
- Intellectual Property
- Life Sciences
- Materials
- Tech Scout
- Unparalleled Data Quality
- Higher Quality Content
- 60% Fewer Hallucinations
Browse by: Latest US Patents, China's latest patents, Technical Efficacy Thesaurus, Application Domain, Technology Topic, Popular Technical Reports.
© 2025 PatSnap. All rights reserved.Legal|Privacy policy|Modern Slavery Act Transparency Statement|Sitemap|About US| Contact US: help@patsnap.com