Laboratory ore grinding method for unevenly inlaid gold ore
A laboratory and gold mine technology, applied in chemical instruments and methods, wet separation, solid separation, etc., can solve problems such as uneven distribution, improve the grinding effect, prevent over-grinding or under-grinding, and achieve good floating. The effect of selecting particle size conditions
- Summary
- Abstract
- Description
- Claims
- Application Information
AI Technical Summary
Problems solved by technology
Method used
Image
Examples
Embodiment 1
[0029] A gold mine contains 1.85g / t of gold, 1.06% of sulfur, 5.86% of iron, 16.66% of CaO, 6.48% of MgO, and 6.48% of Al 2 o 3 7.70%, containing SiO 2 38.56%. The gold distribution rate of +75μm particle size is 24%, the distribution rate of -75μm+53μm particle size gold is 12%, the distribution rate of -53μm+38μm particle size gold is 14%, and the distribution rate of -38μm particle size gold is 50%. A laboratory rod mill (Φ200mm×160mm) is used to grind the incoming gold ore feed (grain size -2mm accounts for 100%), and after grinding to -75μm accounts for 80%, the material is discharged to obtain pulp 1. Then use a 38 μm standard sieve to screen the pulp 1 and divide it into a particle size above +38 μm and a particle size below -38 μm. The particle size above +38 μm enters the rod mill (Φ200mm×160mm) again for grinding, and after grinding to +75 μm, accounting for 10% of the raw ore, the material is discharged to obtain the pulp 2. The particle size below -38 μm is mix...
Embodiment 2
[0034] A gold mine contains 4.68g / t of gold, 1.54% of sulfur, 8.06% of iron, 9.57% of CaO, 3.16% of MgO, and 3.16% of Al 2 o 3 15.52%, containing SiO 2 49.71%. The gold distribution rate of +75μm particle size is 25%, the distribution rate of -75μm+53μm particle size gold is 14%, the distribution rate of -53μm+38μm particle size gold is 15%, and the distribution rate of -38μm particle size gold is 46%. A laboratory ball mill (Φ240mm×90mm) is used to grind the incoming gold ore feed (grain size -2mm, accounting for 100%), and after grinding to -75μm, accounting for 80%, the material is discharged to obtain the pulp 1. Then use a 38 μm standard sieve to screen the pulp 1 and divide it into a particle size above +38 μm and a particle size below -38 μm. The particle size above +38 μm enters the ball mill (Φ240mm×90mm) again for grinding, and the material is discharged after grinding to +75 μm, accounting for 10% of the raw ore, to obtain pulp 2. The particle size below -38 μm ...
PUM
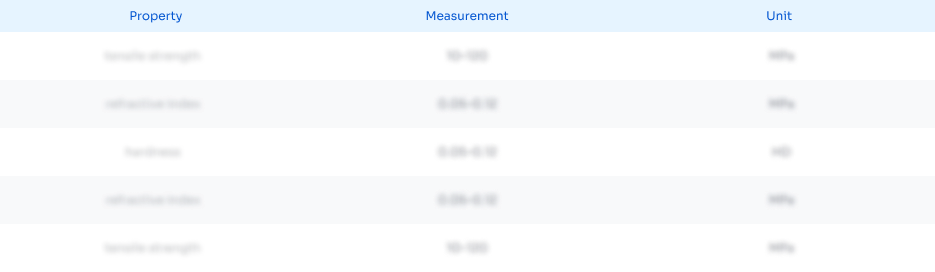
Abstract
Description
Claims
Application Information

- R&D
- Intellectual Property
- Life Sciences
- Materials
- Tech Scout
- Unparalleled Data Quality
- Higher Quality Content
- 60% Fewer Hallucinations
Browse by: Latest US Patents, China's latest patents, Technical Efficacy Thesaurus, Application Domain, Technology Topic, Popular Technical Reports.
© 2025 PatSnap. All rights reserved.Legal|Privacy policy|Modern Slavery Act Transparency Statement|Sitemap|About US| Contact US: help@patsnap.com