Electrical discharge machining apparatus, and method for controlling jump operation
An electrical discharge machining and action technology, applied in electric machining equipment, metal machining equipment, circuits, etc., can solve the problems of reduced machining efficiency, shortened lifting and lowering time, and increased machining interruption time, so as to achieve the effect of high-efficiency electric discharge machining.
- Summary
- Abstract
- Description
- Claims
- Application Information
AI Technical Summary
Problems solved by technology
Method used
Image
Examples
Embodiment approach 1
[0022] figure 1 It is a block diagram showing a configuration example of the electrical discharge machining device 1 according to Embodiment 1 of the present invention. The electrical discharge machining device 1 has a material information input unit 2, a processing condition input unit 3, a storage unit 4, a comparison unit 5, a lifting parameter adjustment unit 6, a lifting action control unit 7, a discharge pulse detection unit 8, a discharge pulse number accumulation unit 9, Z-axis motor control unit 10 , Z-axis motor 11 , machining power supply control unit 12 , machining unit 13 , machining speed calculation unit 14 , machining actual record storage unit 15 and update unit 16 . The processing part 13 has: the electrode 131 used for electric discharge machining, and the workpiece 132 which becomes the processing object of electric discharge machining.
[0023] The material information input unit 2 receives input of information on the material of the electrode 131 and inf...
Embodiment approach 2
[0068] In Embodiment 1, the electric discharge machining device 1 stores the optimum value determined according to the combination of the electrode material and the workpiece material, and updates the optimum value appropriately in order to maximize the machining efficiency. However, the optimum value is affected by the processing area, processing conditions, etc. in addition to the combination of the electrode material and the material of the workpiece. In Embodiment 2, the electrical discharge machining device stores optimum values determined according to combinations of electrode materials and workpiece materials, machining areas, and machining conditions, and appropriately updates the optimum values in order to maximize machining efficiency. Differences from Embodiment 1 will be described.
[0069] Image 6 It is a block diagram showing a configuration example of the electrical discharge machining device 1 a according to the second embodiment. Electrical discharge ma...
PUM
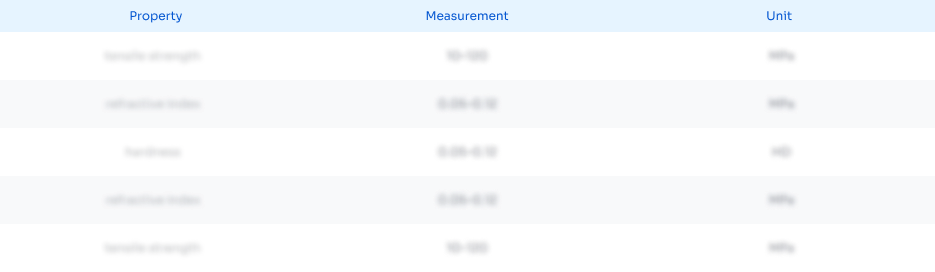
Abstract
Description
Claims
Application Information

- R&D Engineer
- R&D Manager
- IP Professional
- Industry Leading Data Capabilities
- Powerful AI technology
- Patent DNA Extraction
Browse by: Latest US Patents, China's latest patents, Technical Efficacy Thesaurus, Application Domain, Technology Topic, Popular Technical Reports.
© 2024 PatSnap. All rights reserved.Legal|Privacy policy|Modern Slavery Act Transparency Statement|Sitemap|About US| Contact US: help@patsnap.com