Holder assembly double threaded hole machining method and double-order single-screw tap used for same
A hole processing method and cage technology, which are applied in thread cutting tools, metal processing equipment, manufacturing tools, etc., can solve the problems of inconsistent end face clearance of rolling elements, clamping of rolling elements, and unstable installation, and improve high-precision matching. Group requirements, continuous service life improvement, effect of saving machining time
- Summary
- Abstract
- Description
- Claims
- Application Information
AI Technical Summary
Problems solved by technology
Method used
Image
Examples
Embodiment Construction
[0030] Attached below Figure 1-6 The specific embodiment of the present invention will be further described.
[0031] A method for processing double threaded holes of a cage assembly includes the following steps:
[0032] A. The upper and lower cage components are fixed on the rotary table of the CNC drilling machine with a fixture, and the bottom supporting base 11 and the intermediate process washer 9 are clamped and fixed by the pressure plate;
[0033] B. Clamp the second-order drill bit 7 on the CNC drilling machine, process the light holes ΦD1 and ΦD2 of the upper and lower cage components in a single time; retract the tool; after the workbench rotates and divide it into equal parts, repeat the continuous operation until all the light holes are completed;
[0034] C. Use the tap chuck to replace the double-stage single-spiral tap. The double-stage single-spiral tap enters from top to bottom, and the first-stage tap 2 enters the lower cage 10 through the upper light hol...
PUM
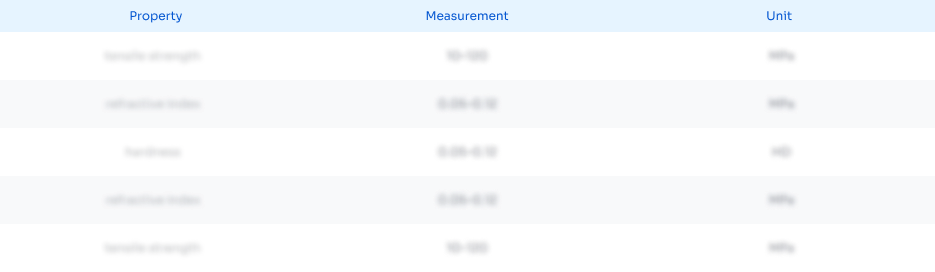
Abstract
Description
Claims
Application Information

- R&D
- Intellectual Property
- Life Sciences
- Materials
- Tech Scout
- Unparalleled Data Quality
- Higher Quality Content
- 60% Fewer Hallucinations
Browse by: Latest US Patents, China's latest patents, Technical Efficacy Thesaurus, Application Domain, Technology Topic, Popular Technical Reports.
© 2025 PatSnap. All rights reserved.Legal|Privacy policy|Modern Slavery Act Transparency Statement|Sitemap|About US| Contact US: help@patsnap.com