Method for strongly deforming and rolling bimetallic composite plate
A bimetal and clad plate technology, applied in metal rolling, metal rolling, metal processing equipment and other directions, can solve the problems of low bonding strength, warpage, large residual stress, etc., and achieve the effect of improving bonding strength and promoting outflow.
- Summary
- Abstract
- Description
- Claims
- Application Information
AI Technical Summary
Problems solved by technology
Method used
Image
Examples
Embodiment 1
[0032] refer to Figure 1-3 , 5, 6, a kind of cold-rolling method of preparing Cu / Al bimetal clad plate, comprises the following steps:
[0033] S1. Blank making: select pure Al plate as substrate 1, with length, width, and height of 50mm, 50mm, and 3mm respectively, and select pure Cu plate as double plate 2, with length, width, and height of 50mm, 50mm, and 1mm, respectively. The deformation resistance of Al plate is relatively high. Small, the deformation resistance of the Cu plate is relatively large, the ratio of the thickness of the base plate 1 to the double plate 2 is 3, and the double plate 2 is stacked on the top of the base plate 1, symmetrically at a distance of 25mm in the width direction of the rolled bite end. Drilling two holes and riveting them with rivets can ensure that the component plates of the bimetallic composite slab 3 can be bitten into the rolls synchronously to obtain the bimetallic composite slab 3 . In this embodiment, the thickness ratio of the ...
Embodiment 2
[0039] refer to figure 1 , 2 , 4-6, a kind of warm rolling method for preparing Mg / Al bimetal clad plate, comprises the following steps:
[0040] S1. Blank making: choose 5052 grade aluminum alloy plate as the substrate 1, the length, width and height are 50mm, 50mm, 3mm respectively, choose AZ31 grade magnesium alloy plate as the double board 2, the length, width and height are 50mm, 50mm, 1mm, respectively, 5052 grade The deformation resistance of the aluminum alloy plate is small, and the deformation resistance of the AZ31 magnesium alloy plate is relatively large. The ratio of the thickness of the substrate 1 to the double plate 2 is 3. The double plate 2 is stacked on the top of the base plate 1. Two holes are symmetrically drilled at a distance of 25mm in the width direction of the entry end and riveted with rivets to obtain a bimetallic composite panel slab 3 . In this embodiment, the thickness ratio of the substrate 1 and the doubler board 2 is 3, and in other embodi...
PUM
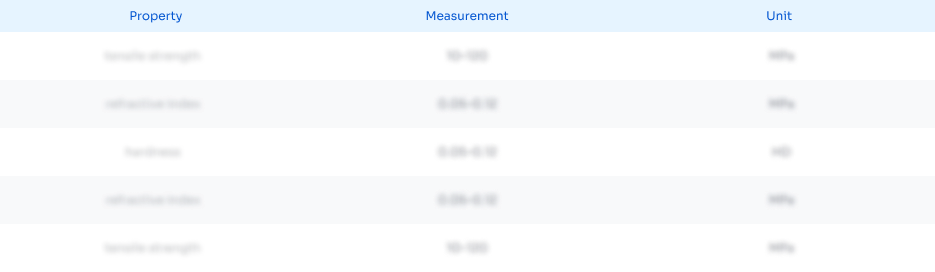
Abstract
Description
Claims
Application Information

- R&D
- Intellectual Property
- Life Sciences
- Materials
- Tech Scout
- Unparalleled Data Quality
- Higher Quality Content
- 60% Fewer Hallucinations
Browse by: Latest US Patents, China's latest patents, Technical Efficacy Thesaurus, Application Domain, Technology Topic, Popular Technical Reports.
© 2025 PatSnap. All rights reserved.Legal|Privacy policy|Modern Slavery Act Transparency Statement|Sitemap|About US| Contact US: help@patsnap.com