A method of recovering tartaric acid from calcium tartrate using interfacial reaction
A calcium tartrate and interfacial reaction technology, applied in the chemical field, can solve the problems of low recycling cost, high cost, and high energy consumption in the recycling process, and achieve the effects of low recycling cost, improved purity and yield, and shortened concentration time
- Summary
- Abstract
- Description
- Claims
- Application Information
AI Technical Summary
Problems solved by technology
Method used
Examples
Embodiment 1
[0019] In a 100L glass-lined reaction kettle, add 60kg of dioxane, 4.1kg of 98% sulfuric acid and stir, add about 8.57kg of calcium tartrate solid in batches, control the temperature in the kettle at 60°C, and stir at 60°C for 2 hours after the addition is completed. Suction filtration to remove impurities such as insoluble inorganic salt calcium sulfate, let stand, collect tartaric acid dioxane mother liquor to the storage tank, or directly transfer to the concentration kettle. Recover the solvent by distillation under normal pressure or reduced pressure, control the final vacuum degree to -0.07~-0.1Mpa, T ≤ 80°C, dry at 55~80°C for 4~6 hours, and obtain the tartaric acid product. Solvent applied with the next batch. The yield of recovered tartaric acid is 96.3%. After analysis: HPLC content ≥99%, melting point: 169-171°C.
Embodiment 2
[0021] In a 100L glass-lined reaction kettle, add 40kg of butanone, 9.5kg of 98% sulfuric acid and stir, add about 20kg of calcium tartrate solid in batches, control the temperature in the kettle to 80°C, and stir at 80°C for 1hr after the addition is completed. Suction filtration to remove impurities such as insoluble inorganic salt calcium sulfate, let stand, collect tartaric acid dioxane mother liquor to the storage tank, or directly transfer to the concentration kettle. Recover the solvent by distillation under normal pressure or reduced pressure, control the final vacuum degree to -0.07~-0.1Mpa, T ≤ 80°C, dry at 55~80°C for 4~6 hours, and obtain the tartaric acid product. Solvent applied with the next batch. The yield of recovered tartaric acid is 95.6%. After analysis, the HPLC content is ≥98.5%, and the melting point is 169-171°C.
Embodiment 3
[0023] In a 100L glass-lined reactor, add 50kg of dioxane, 5.5kg of 85% phosphoric acid and stir, add about 10kg of calcium tartrate solid in batches, control the temperature in the kettle to 70°C, and stir at 70°C for 1.5hr after the addition. Suction filtration to remove impurities such as insoluble inorganic salt calcium sulfate, let stand, collect tartaric acid dioxane mother liquor to the storage tank, or directly transfer to the concentration kettle. Recover the solvent by distillation under normal pressure or reduced pressure, control the final vacuum degree to -0.07~-0.1Mpa, T ≤ 80°C, dry at 55~80°C for 4~6 hours, and obtain the tartaric acid product. Solvent applied with the next batch. The yield of recovered tartaric acid is 94%. After analysis, the HPLC content is ≥98.2%, and the melting point is 169-171°C.
PUM
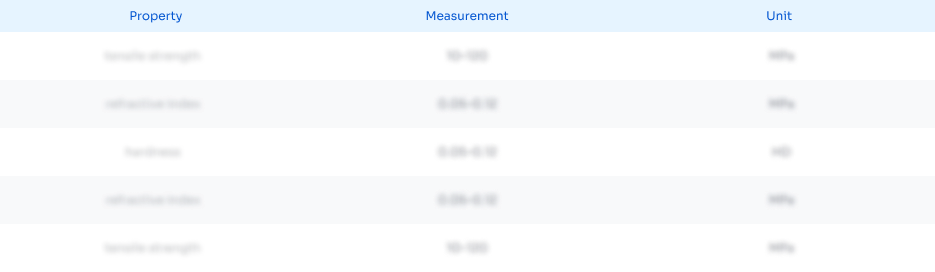
Abstract
Description
Claims
Application Information

- Generate Ideas
- Intellectual Property
- Life Sciences
- Materials
- Tech Scout
- Unparalleled Data Quality
- Higher Quality Content
- 60% Fewer Hallucinations
Browse by: Latest US Patents, China's latest patents, Technical Efficacy Thesaurus, Application Domain, Technology Topic, Popular Technical Reports.
© 2025 PatSnap. All rights reserved.Legal|Privacy policy|Modern Slavery Act Transparency Statement|Sitemap|About US| Contact US: help@patsnap.com