Spaceflight load vibration reducing box for rocket launching conditions
A technology of rocket launching and damping box, which is applied to the design features of spring/shock absorber, spring/shock absorber, and non-rotational vibration suppression. Vibration effect, vibration performance improvement, and the effect of reducing transient acceleration impact
Pending Publication Date: 2019-12-20
SHENYANG INST OF AUTOMATION - CHINESE ACAD OF SCI
View PDF0 Cites 4 Cited by
- Summary
- Abstract
- Description
- Claims
- Application Information
AI Technical Summary
Problems solved by technology
This complex vibration environment will cause the performance accuracy of the components in the microinj
Method used
the structure of the environmentally friendly knitted fabric provided by the present invention; figure 2 Flow chart of the yarn wrapping machine for environmentally friendly knitted fabrics and storage devices; image 3 Is the parameter map of the yarn covering machine
View moreImage
Smart Image Click on the blue labels to locate them in the text.
Smart ImageViewing Examples
Examples
Experimental program
Comparison scheme
Effect test
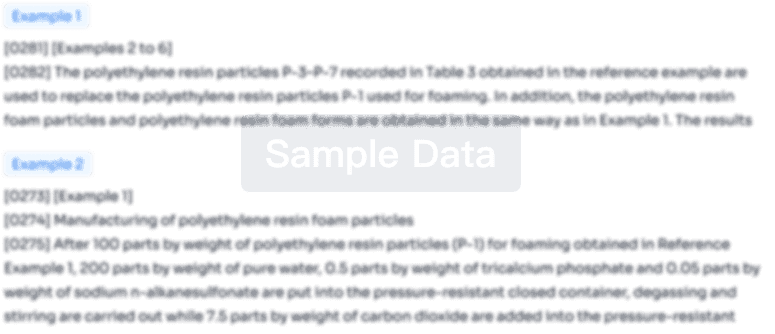
PUM
Property | Measurement | Unit |
---|---|---|
Density | aaaaa | aaaaa |
Thickness | aaaaa | aaaaa |
Login to View More
Abstract
The invention belongs to the vibration control and vibration reducing technology field, and particularly relates to a spaceflight load vibration reducing box for rocket launching conditions. The spaceflight load vibration reducing box for the rocket launching conditions comprises a box body, a primary vibration reducing structure, a secondary vibration reducing structure, a macro manipulator, a box body mounting tool and an acceleration sensor, wherein the bottom of the box body is connected with the box body mounting tool through the primary vibration reducing structure, the macro manipulatoris arranged in the box body through the secondary vibration reducing structure, the first vibration reducing structure is used for reducing high frequency vibration response, the secondary vibrationreducing structure is used for reducing vibration of low frequency resonance response, and the acceleration sensor is arranged on the macro manipulator and used for acquiring vibration signals under the corresponding vibration conditions. The spaceflight load vibration reducing box for the rocket launching conditions can perform effective vibration reducing on a test instrument through the secondary passive vibration reducing technology, thereby effectively protecting the test instrument, and the design of the vibration reducing box and a test method thereof can provide reference to related fields, and play a critical part in vibration reducing protection of a space science load launching segment.
Description
technical field [0001] The invention belongs to the technical field of vibration control and vibration reduction, in particular to an aerospace load vibration reduction box used in rocket launch conditions. Background technique [0002] In the exploration of space life, the current research at home and abroad is mainly to study the survival of space cells through some bacteria and cell culture methods, but there is no report on the use of microinjection to intervene in the later development of cells and embryos. However, entering space after injection on the ground will be affected by factors such as the launch process. If the microinjection experiment can be carried out in the space environment, the introduction of other influencing factors such as the launch process can be eliminated, and the ground operation and the control experiment of the post-injection development process in the space microgravity environment can be carried out. It is of great significance to protect...
Claims
the structure of the environmentally friendly knitted fabric provided by the present invention; figure 2 Flow chart of the yarn wrapping machine for environmentally friendly knitted fabrics and storage devices; image 3 Is the parameter map of the yarn covering machine
Login to View More Application Information
Patent Timeline

IPC IPC(8): F16F15/02F16F15/08F16F3/093F16F3/087
CPCF16F3/0876F16F3/093F16F15/02F16F15/08F16F2230/08
Inventor 骆海涛王浩楠刘广明于长帅富佳王昊辰
Owner SHENYANG INST OF AUTOMATION - CHINESE ACAD OF SCI
Features
- R&D
- Intellectual Property
- Life Sciences
- Materials
- Tech Scout
Why Patsnap Eureka
- Unparalleled Data Quality
- Higher Quality Content
- 60% Fewer Hallucinations
Social media
Patsnap Eureka Blog
Learn More Browse by: Latest US Patents, China's latest patents, Technical Efficacy Thesaurus, Application Domain, Technology Topic, Popular Technical Reports.
© 2025 PatSnap. All rights reserved.Legal|Privacy policy|Modern Slavery Act Transparency Statement|Sitemap|About US| Contact US: help@patsnap.com