Artificial microcrystalline pumice material and method for preparing artificial microcrystalline pumice material from industrial solid waste by volcanic diagenesis method at low temperature
A technology of industrial solid waste and artificial micro-pumice, applied in the field of artificial micro-crystalline pumice materials and low-temperature preparation of artificial micro-crystalline pumice materials from industrial solid waste by volcanic diagenesis, which can solve the problems of low water absorption, low thermal conductivity, supply shortage, etc., and achieve water absorption. Low-cost, versatile, and high-performance effects
- Summary
- Abstract
- Description
- Claims
- Application Information
AI Technical Summary
Problems solved by technology
Method used
Image
Examples
Embodiment 1
[0025] The raw material ratio (percentage by weight, the same below) of the artificial microcrystalline pumice material is as shown in table 1:
[0026] The raw material ratio of table 1 artificial microcrystalline pumice material
[0027]
[0028] Among the above raw materials, the weight ratio of the components is: Al 2 o 3 : SiO 2 : CaO: MgO: Fe 2 o 3 :K 2 O: Na 2 O=5:70:4:4:9:3:1.
[0029] The artificial microcrystalline pumice material is prepared according to the following steps:
[0030] 1. Select the raw materials shown in Table 1.
[0031] 2. The raw materials selected in step 1 were weighed according to the proportion shown in Table 1, mixed, and ground in a ball mill with a fineness of 30 microns to obtain raw meal powder.
[0032] 3. Stamping the raw meal powder prepared in step 2.
[0033] 4. Sinter the shaped raw meal prepared in step 3 in a tunnel kiln, set the maximum firing temperature to 900°C, and the heating rate to 10°C / min.
[0034] 5. The m...
Embodiment 2
[0037] The ratio of raw materials of artificial microcrystalline pumice material is as shown in table 2:
[0038] The raw material ratio of table 2 artificial microcrystalline pumice material
[0039]
[0040] Among the above raw materials, the weight ratio of the components is: Al 2 o 3 : SiO 2 : CaO: MgO: Fe 2 o 3 :K 2 O: Na 2 O=10:72:3:3:4:1:2.
[0041] The artificial microcrystalline pumice material is prepared according to the following steps:
[0042] 1. Select the raw materials shown in Table 2.
[0043] 2. The raw materials selected in step 1 are weighed according to the proportion shown in Table 2, mixed, and ground in a ball mill to control the particle size to about 25 microns to obtain raw meal powder.
[0044] 3. Extrude the raw meal powder prepared in step 2.
[0045] 4. The shaped raw meal prepared in step 3 is sintered in a roller kiln, the maximum firing temperature is set at 850°C, and the heating rate is 15°C / min.
[0046] 5. The material obtai...
Embodiment 3
[0049] The raw material ratio of artificial microcrystalline pumice material is as shown in table 3:
[0050] The raw material ratio of table 3 artificial microcrystalline pumice material 1
[0051]
[0052]
[0053] Among the above raw materials, the weight ratio of the components is: Al 2 o 3 : SiO 2 : CaO: MgO: Fe 2 o 3 :K 2 O: Na 2 O=10:65:5:3:6:1:2.
[0054] The artificial microcrystalline pumice material is prepared according to the following steps:
[0055]1. Select the raw materials shown in Table 3.
[0056] 2. The raw materials selected in step 1 are weighed according to the proportion shown in Table 3, mixed, and ground in a ball mill to control the particle size to about 35 microns to obtain raw meal powder.
[0057] 3. Extrude the raw meal powder prepared in step 2.
[0058] 4. Put the molding raw material prepared in step 3 in 1m 3 Sintering in a shuttle kiln with a maximum firing temperature of 980°C and a heating rate of 12°C / min.
[0059] 5. ...
PUM
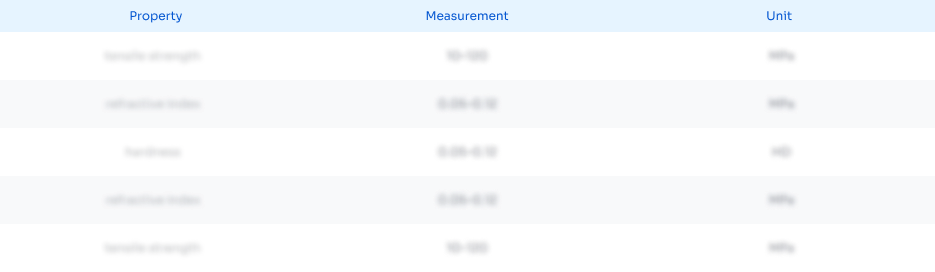
Abstract
Description
Claims
Application Information

- Generate Ideas
- Intellectual Property
- Life Sciences
- Materials
- Tech Scout
- Unparalleled Data Quality
- Higher Quality Content
- 60% Fewer Hallucinations
Browse by: Latest US Patents, China's latest patents, Technical Efficacy Thesaurus, Application Domain, Technology Topic, Popular Technical Reports.
© 2025 PatSnap. All rights reserved.Legal|Privacy policy|Modern Slavery Act Transparency Statement|Sitemap|About US| Contact US: help@patsnap.com