A concrete preparation process
A preparation process, concrete technology, applied in the field of concrete preparation process, can solve problems such as weak strength, affecting concrete workability, strength and durability, and insufficient hydration of cementitious materials, so as to facilitate disassembly and degradation, and improve hydration Product distribution state, effect of improving microscopic uniformity
- Summary
- Abstract
- Description
- Claims
- Application Information
AI Technical Summary
Problems solved by technology
Method used
Image
Examples
Embodiment 1
[0042] refer to figure 1 , is a kind of concrete preparation technology disclosed by the present invention, and it comprises the following processing steps:
[0043] S1: After mixing water and surface wetting agent evenly, put in fine aggregate, and stir at a speed of 40r / min for 10s to prepare the first mixture; the weight ratio of water, fine aggregate and surface wetting agent is 1:3:0.01;
[0044] The fine aggregate comprises the following raw materials in weight percentage: 30% machine-made sand and 70% natural sand;
[0045] The surface wetting agent adopts ST-5100 non-ionic gemini surfactant produced by Shanghai Sangjing Chemical Co., Ltd.;
[0046] S2: Add the gel material and dispersant to the first mixture, first stir at a stirring speed of 100r / min for one-third of the total stirring time, then stir at a stirring speed of 60r / min for the remaining two-thirds of the time , the total stirring time is 20s, after stirring evenly, the second mixture is prepared; the w...
Embodiment 1
[0061] The difference between embodiment 10-13 and embodiment 1 is that the weight ratio of fine aggregate, coarse aggregate, fiber filler and water in step 3 is as shown in the table below:
[0062]
[0063]
[0064] The difference between embodiment 14-17 and embodiment 1 is that the weight ratio of admixture and fine aggregate in step 4 is as shown in the following table:
[0065]
[0066] The difference between embodiment 18-21 and embodiment 1 is that the fine aggregate comprises the following raw materials in weight percent:
[0067]
[0068] The difference between Embodiment 22-25 and Embodiment 1 is that the gel material comprises the following raw materials in weight percentage:
[0069]
[0070] The difference between Examples 26-29 and Example 1 is that the content of needle-shaped coarse aggregate in the coarse aggregate is shown in the table below:
[0071]
[0072]
[0073] The difference between embodiments 30-33 and embodiment 1 is that th...
PUM
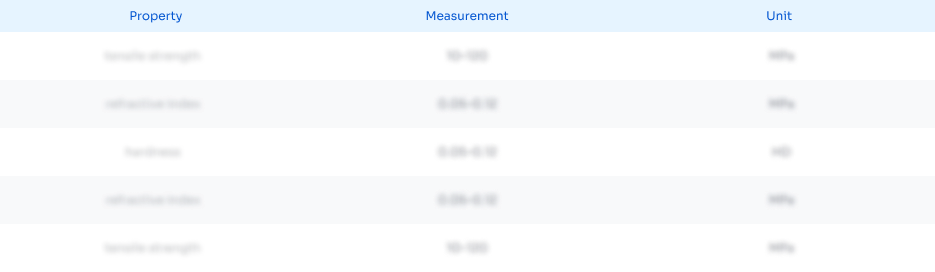
Abstract
Description
Claims
Application Information

- R&D
- Intellectual Property
- Life Sciences
- Materials
- Tech Scout
- Unparalleled Data Quality
- Higher Quality Content
- 60% Fewer Hallucinations
Browse by: Latest US Patents, China's latest patents, Technical Efficacy Thesaurus, Application Domain, Technology Topic, Popular Technical Reports.
© 2025 PatSnap. All rights reserved.Legal|Privacy policy|Modern Slavery Act Transparency Statement|Sitemap|About US| Contact US: help@patsnap.com