Method for outputting measured exciting force signal of piezoelectric vibration sensor with high sensitivity
A high-sensitivity, exciting force technology, applied to the measurement of the property force of piezoelectric devices, instruments, measuring devices, etc., can solve the problems of inaccurate measurement of high-frequency vibration signals, achieve high damping, improve linearity, Effect of high frequency cap
- Summary
- Abstract
- Description
- Claims
- Application Information
AI Technical Summary
Problems solved by technology
Method used
Image
Examples
Embodiment Construction
[0014] refer to figure 1 . According to the present invention, the piezoelectric cantilever 3 is fixed by the base 5, one end is fixed on the base 5, and the other end is suspended to fix the mass 1; the piezoelectric cantilever 3 is formed by overlapping at least two piezoelectric sensitive elements as a sensitive element. The vibration of the mass block 1 to be measured acts on the sensitive element, and the resulting cantilever beam fixes a damping block 4 at a position close to the base 5; the piezoelectric body of the cantilever beam vibrates under the action of the mass block 1, and the vibration frequency is close to At the first-order resonance frequency of the piezoelectric body of the cantilever beam, the damping of the damping block 4 acts on the piezoelectric cantilever beam 3, suppressing the sharp increase of the amplitude resonance near the first-order resonance frequency point of the bending vibration mode of the cantilever beam, and obtaining a higher upper fr...
PUM
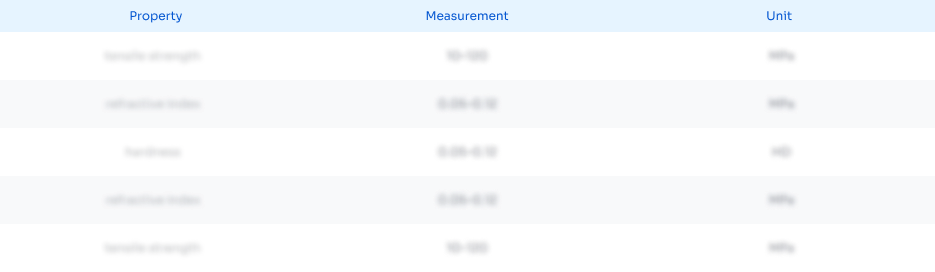
Abstract
Description
Claims
Application Information

- R&D
- Intellectual Property
- Life Sciences
- Materials
- Tech Scout
- Unparalleled Data Quality
- Higher Quality Content
- 60% Fewer Hallucinations
Browse by: Latest US Patents, China's latest patents, Technical Efficacy Thesaurus, Application Domain, Technology Topic, Popular Technical Reports.
© 2025 PatSnap. All rights reserved.Legal|Privacy policy|Modern Slavery Act Transparency Statement|Sitemap|About US| Contact US: help@patsnap.com