Energy-saving and emission-reducing hydrogen gas classified injection method for sintering
A gas classification, energy saving and emission reduction technology, applied in the field of iron and steel metallurgy, can solve the problems of deterioration of sinter reducibility, low sinter strength, short residence time, etc., and achieve the goal of improving heat utilization efficiency, drum strength and quality Effect
- Summary
- Abstract
- Description
- Claims
- Application Information
AI Technical Summary
Problems solved by technology
Method used
Image
Examples
Embodiment 1
[0025] A sintering energy-saving and emission-reducing hydrogen-based gas staged injection technology, under the conditions of 5.6% carbon content of the mixture, 1.85 binary basicity, 6.75% sintering moisture, sintering negative pressure -10kPa, and 700mm layer height, the sintering material The area between the surface and the position where the highest temperature is 1250 °C is area I, the area between 1250 °C and 1300 °C is area II, and the area between 1300 °C and 1350 °C is area III. Reduce the carbon content of the mixture to 5.3%, and under the sintering cup test with the same other conditions, according to the heat replacement ratio of the added gas fuel and the reduced solid fuel of 1:4.5, the sequential injection heat value in areas Ⅰ, Ⅱ, and Ⅲ is 39.8 MJ / Nm 3 The injection height is 450mm. The natural gas supplement in zone I accounts for 50% of the total heat supplement, the natural gas supplement in zone II accounts for 30% of the total heat supplement, and the n...
Embodiment 2
[0027]Reduce the carbon content of the mixture to 5.15%, and under the same sintering test under the other conditions, according to the heat replacement ratio of 1:4 between the added gas fuel and the reduced solid fuel, the heat value of sequential injection in areas Ⅰ, Ⅱ, and Ⅲ is 39.8MJ / Nm 3 Natural gas is used for compensation, and the injection height is 500mm. The natural gas supplement in area I accounts for 55% of the total heat supplement, the natural gas supplement in area II accounts for 30% of the total heat supplement, and the natural gas supplement in area III accounts for 55% of the total heat supplement. 15% of total caloric intake. Sintering index, NO X , SO 2 and CO X The emission reductions are shown in Table 1.
Embodiment 3
[0029] Reduce the carbon content of the mixture to 5.0%, and under the same sintering test with other conditions, according to the heat replacement ratio of added gas fuel and reduced solid fuel of 1:3.5, the heat value of sequential injection in areas I, II, and III is 39.8MJ / Nm 3 The injection height is 550mm. The natural gas supplement in area I accounts for 60% of the total heat supplement, the natural gas supplement in area II accounts for 30% of the total heat supplement, and the natural gas supplement in area III accounts for 60% of the total heat supplement. 10% of total caloric intake. Sintering index, NO X , SO 2 and CO X The emission reductions are shown in Table 1.
PUM
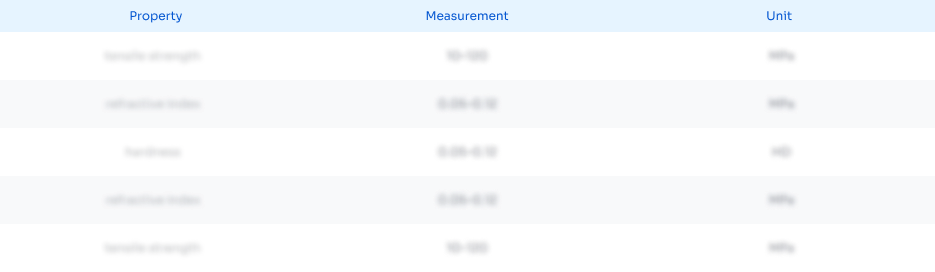
Abstract
Description
Claims
Application Information

- R&D
- Intellectual Property
- Life Sciences
- Materials
- Tech Scout
- Unparalleled Data Quality
- Higher Quality Content
- 60% Fewer Hallucinations
Browse by: Latest US Patents, China's latest patents, Technical Efficacy Thesaurus, Application Domain, Technology Topic, Popular Technical Reports.
© 2025 PatSnap. All rights reserved.Legal|Privacy policy|Modern Slavery Act Transparency Statement|Sitemap|About US| Contact US: help@patsnap.com