Pretreatment method of straw lignocelluloses raw material
A lignocellulose and pretreatment technology, which is applied in biofuel, fermentation and other directions, can solve the problems of high catalyst preparation cost and high solvent cost, and achieve the effect of promoting industrialization process, simple operation and low energy consumption
- Summary
- Abstract
- Description
- Claims
- Application Information
AI Technical Summary
Problems solved by technology
Method used
Image
Examples
specific Embodiment approach 1
[0015] Specific embodiment one: the pretreatment method of the straw lignocellulose raw material of the present embodiment is carried out according to the following steps:
[0016] 1. Crush the air-dried straw into straw powder and dry to constant weight;
[0017] 2. Prepare H with distilled water 3 PW 12 o 40 aqueous solution, the straw powder and H 3 PW 12 o 40 Mix the solution evenly, place it in an open tray, then transfer the tray to a blast drying oven, heat up to 105-110°C for 1h-4h, and complete the first stage of heating treatment; then raise the temperature to 130°C-160°C Heating for 20min to 60min to complete the second stage of heating treatment;
[0018] 3. Cool down to room temperature after heating, take out the product, add distilled water to the product several times to stir, suction filter, collect solid residue and filtrate; wherein the solid residue is straw lignocellulose that has completed the pretreatment; add ether to the filtrate, Shake, collect...
specific Embodiment approach 2
[0019] Embodiment 2: The difference between this embodiment and Embodiment 1 is that the fineness of the straw powder in step 1 is 40-80 mesh; others are the same as Embodiment 1.
specific Embodiment approach 3
[0020] Embodiment 3: The difference between this embodiment and Embodiment 1 or 2 is that the drying temperature in step 1 is 60-70° C.; the others are the same as Embodiment 1 or 2.
PUM
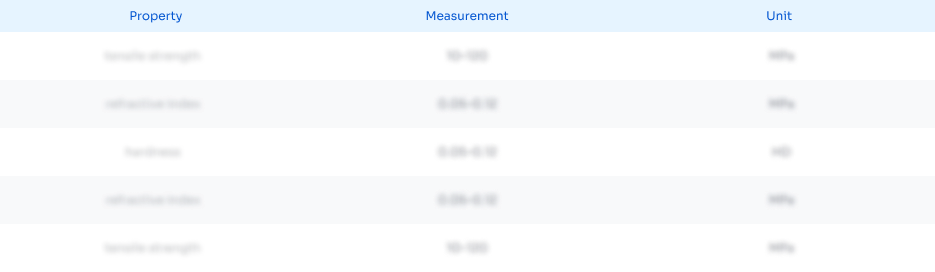
Abstract
Description
Claims
Application Information

- R&D
- Intellectual Property
- Life Sciences
- Materials
- Tech Scout
- Unparalleled Data Quality
- Higher Quality Content
- 60% Fewer Hallucinations
Browse by: Latest US Patents, China's latest patents, Technical Efficacy Thesaurus, Application Domain, Technology Topic, Popular Technical Reports.
© 2025 PatSnap. All rights reserved.Legal|Privacy policy|Modern Slavery Act Transparency Statement|Sitemap|About US| Contact US: help@patsnap.com