Water permeable brick manufactured by sintering of urban sludge and construction waste and manufacturing method of water permeable brick
A technology for construction waste and urban sludge, applied in applications, household appliances, clay products, etc., can solve problems such as affecting the urban living environment, easily generating dust, occupying land, etc., and achieving a wide source of raw materials, low cost, and enhanced performance. Effect
- Summary
- Abstract
- Description
- Claims
- Application Information
AI Technical Summary
Problems solved by technology
Method used
Examples
Embodiment 1
[0031] 1) Municipal sludge drying pretreatment: drying the municipal sludge to a moisture content of 30%;
[0032] 2) Construction waste and shale treatment: the construction waste and shale are initially mixed and crushed, and then further crushed, mixed and ground to 60 mesh;
[0033] 3) Aging treatment: Mix 10 parts of municipal sludge, 40 parts of shale, and 30 parts of construction waste after step 1) and step 2), and add 15 parts of water to fully mix, and age the mixture after mixing. Chemical treatment, the mixture aging time is 24h;
[0034] 4) Extrusion molding: the aged mixture is fed into a vacuum brick extruder to form a billet under pressure, and the molding extrusion pressure is 15Mpa;
[0035] 5) Brick drying: Send the formed bricks into the drying kiln for drying. The drying time of the bricks is 25 hours, the drying temperature is 170°C, and the moisture content of the bricks after drying is 5-8%;
[0036] 6) High-temperature roasted finished products: the ...
Embodiment 2
[0038] 1) Municipal sludge drying pretreatment: drying the municipal sludge to a moisture content of 33%;
[0039] 2) Construction waste and shale treatment: the construction waste and shale are initially mixed and crushed, and then further crushed, mixed and ground to 70 mesh;
[0040] 3) Aging treatment: Mix 13 parts of municipal sludge, 44 parts of shale, and 34 parts of construction waste after step 1) and step 2), and add 15 parts of water to fully mix, and age the mixture after mixing. Chemical treatment, the mixture aging time is 28h;
[0041] 4) Extrusion molding: the aged mixture is fed into a vacuum brick extruder to form a billet under pressure, and the molding extrusion pressure is 18Mpa;
[0042] 5) Brick drying: send the shaped bricks into the drying kiln for drying, the drying time of the bricks is 28 hours, the drying temperature is 172°C, and the moisture content of the bricks after drying is 6%;
[0043] 6) High-temperature roasted finished products: the dr...
Embodiment 3
[0045] 1) Municipal sludge drying pretreatment: drying the municipal sludge to a moisture content of 35%;
[0046] 2) Construction waste and shale treatment: the construction waste and shale are initially mixed and crushed, and then further crushed, mixed and ground to 80 mesh;
[0047]3) Aging treatment: Mix 15 parts of municipal sludge, 50 parts of shale, and 35 parts of construction waste after step 1) and step 2), and add 15 parts of water to fully mix, and age the mixture after mixing. Chemical treatment, the mixture aging time is 30h;
[0048] 4) Extrusion molding: the aged mixture is fed into a vacuum brick extruder to form a billet under pressure, and the molding extrusion pressure is 205Mpa;
[0049] 5) Brick drying: Send the formed bricks into the drying kiln for drying. The drying time of the bricks is 30 hours, the drying temperature is 175°C, and the moisture content of the bricks after drying is 6%;
[0050] 6) High-temperature roasted finished products: the dr...
PUM
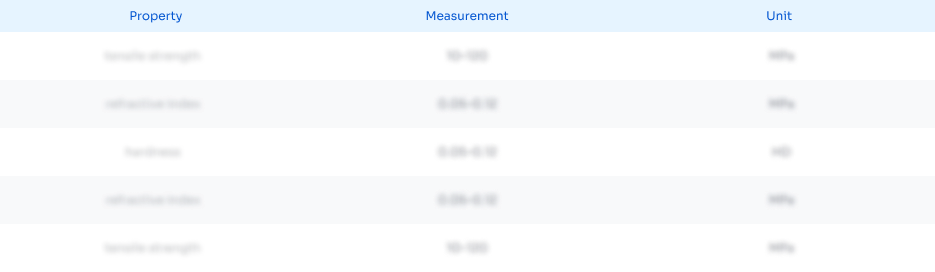
Abstract
Description
Claims
Application Information

- Generate Ideas
- Intellectual Property
- Life Sciences
- Materials
- Tech Scout
- Unparalleled Data Quality
- Higher Quality Content
- 60% Fewer Hallucinations
Browse by: Latest US Patents, China's latest patents, Technical Efficacy Thesaurus, Application Domain, Technology Topic, Popular Technical Reports.
© 2025 PatSnap. All rights reserved.Legal|Privacy policy|Modern Slavery Act Transparency Statement|Sitemap|About US| Contact US: help@patsnap.com