Rubber sole outer skin pattern embossing equipment
A technology for rubber soles and equipment, applied to household appliances, other household appliances, household components, etc., can solve problems such as adverse product effects, reduce product quality, and affect work efficiency, so as to avoid product quality decline, improve work efficiency, and improve The effect of fluency
- Summary
- Abstract
- Description
- Claims
- Application Information
AI Technical Summary
Problems solved by technology
Method used
Image
Examples
Embodiment Construction
[0028] The preferred embodiments of the present invention will be described in detail below in conjunction with the accompanying drawings, so that the advantages and features of the present invention can be more easily understood by those skilled in the art, so as to define the protection scope of the present invention more clearly.
[0029] Examples, see figure 1 , figure 2 , image 3 , Figure 4 , Figure 5 As shown, a rubber shoe sole outer skin pattern pressing equipment includes: a support frame 4, a feed guide roller 6, a feed fixed roller 7, a printing assembly 8, a discharge guide roller 11, and the right side of the support frame 4 from bottom to top. The feed guide roller 6, the feed fixed roller 7, the printing assembly 8 and the printing equipment main body 1 are installed, and the discharge guide roller 11 is installed on the left side;
[0030] The side panel of the main body 1 of the printing equipment is provided with a power control module. The power cont...
PUM
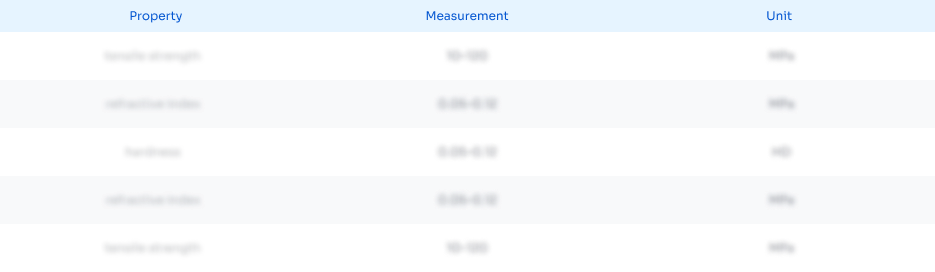
Abstract
Description
Claims
Application Information

- R&D
- Intellectual Property
- Life Sciences
- Materials
- Tech Scout
- Unparalleled Data Quality
- Higher Quality Content
- 60% Fewer Hallucinations
Browse by: Latest US Patents, China's latest patents, Technical Efficacy Thesaurus, Application Domain, Technology Topic, Popular Technical Reports.
© 2025 PatSnap. All rights reserved.Legal|Privacy policy|Modern Slavery Act Transparency Statement|Sitemap|About US| Contact US: help@patsnap.com