A step control method, device, polishing robot and readable storage medium
A technology of step control and robot, which is applied in the fields of grinding robots, readable storage media, devices, and step control methods, and can solve the problems of restricting the precision of grinding, uneven distribution of grinding points, and inability to uniformity of grinding points, etc., to achieve The effect of improving the ability to dynamically correct the grinding position
- Summary
- Abstract
- Description
- Claims
- Application Information
AI Technical Summary
Problems solved by technology
Method used
Image
Examples
Embodiment approach 1
[0031] Such as figure 1 Shown is a step control method for a robot grinding arm, including the following steps:
[0032] Step 1. Locate the preset pose information at the current moment in the grinding track;
[0033] Step 2. Drive the robot grinding arm with grinding blades to feed the grinding blades to the current pre-grinding point according to the preset pose information at the current moment;
[0034] Step 3. Obtain the circumferential force value and axial force value of the polished blade at the current pre-polished point;
[0035] Step 4. Drive the grinding arm of the robot at a variable speed according to the circumferential force value and the axial force value at the current pre-grinding point to feed the grinding blade from the current pre-grinding point to the current deviation-correcting grinding point.
[0036] Before step 1, the grinding trajectory is pre-stored, and the grinding trajectory can be established in the following manner: collect the three-dimens...
Embodiment approach 2
[0044] Such as figure 2 Shown is another step control method for the robot grinding arm, including the following steps:
[0045] Step 1. Locate the preset pose information at the current moment in the grinding track;
[0046] Step 2. Drive the robot grinding arm with grinding blades to feed the grinding blades to the current pre-grinding point according to the preset pose information at the current moment;
[0047] Step 3. Obtain the circumferential force value and axial force value of the polished blade at the current pre-polished point;
[0048] Step 4. According to the circumferential force value and axial force value at the current pre-grinding point, the robot grinding arm is driven at a variable speed to feed the grinding blade from the current pre-grinding point to the current correction grinding point;
[0049] Step 5. Determine whether the sequence position of the preset pose information at the current moment in the grinding trajectory is the last position, if not,...
Embodiment approach 3
[0052] Step 4 specifically includes the following steps:
[0053] Step 41, generating the current shift command according to the circumferential force value at the current pre-grinding point;
[0054] Step 42. According to the axial force value at the current pre-polishing point, the preset pose information at the current moment is corrected into the current correcting pose information of the current correction grinding point in the robot coordinate system;
[0055] Step 43: Drive the grinding arm of the robot at a variable speed according to the current speed change command and the current deviation correction pose information to feed the grinding blade from the current pre-grinding point to the current deviation correction grinding point.
[0056] Specifically, the current speed change command may include an acceleration command for accelerating the driving of the robot grinding arm or an acceleration command for accelerating the driving of the robot grinding arm.
[0057] ...
PUM
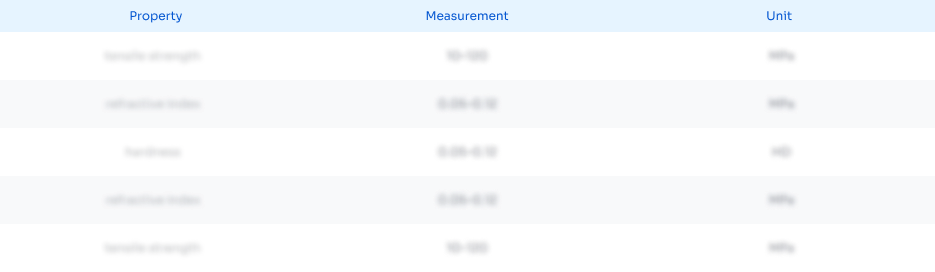
Abstract
Description
Claims
Application Information

- Generate Ideas
- Intellectual Property
- Life Sciences
- Materials
- Tech Scout
- Unparalleled Data Quality
- Higher Quality Content
- 60% Fewer Hallucinations
Browse by: Latest US Patents, China's latest patents, Technical Efficacy Thesaurus, Application Domain, Technology Topic, Popular Technical Reports.
© 2025 PatSnap. All rights reserved.Legal|Privacy policy|Modern Slavery Act Transparency Statement|Sitemap|About US| Contact US: help@patsnap.com