A sucker type magnetorheological damping system and method
A magneto-rheological damping and sucker-type technology, which is applied in the field of dampers, can solve problems such as limited controllable range, poor sealing performance, and large friction force, and achieve contact reliability, detection and damping force, and improved adaptability sexual effect
- Summary
- Abstract
- Description
- Claims
- Application Information
AI Technical Summary
Problems solved by technology
Method used
Image
Examples
Embodiment 1
[0044] Embodiment 1: By designing the magnetorheological fluid 216 bypass, and using the atmospheric pressure and the force sensing function of the piezoelectric sensor 103, a sucker-type magnetorheological damping system is designed, including: a sucker assembly 100, a magnetorheological Damping assembly 200, support assembly 300, controller 400 and connection assembly 500; the suction cup assembly 100 includes: suction cup 101, suction cup seat 102, piezoelectric sensor 103, negative pressure pump 104; the magnetorheological damping assembly 200 includes: Shaft 201, upper end cover 202, lower end cover 203, upper cylinder body 204, lower cylinder body 205, upper damping disc 206, lower damping disc 207, upper gasket 208, lower gasket 207, upper sealing bowl 210, lower sealing bowl 211, upper Guide sleeve 212, lower guide sleeve 213, plunger 214 and coil 215; the support assembly 300 includes: first support 301, second support 302, linear motor 303, support screw 304, motor sh...
Embodiment 2
[0073] The only difference from the first preferred embodiment above is that this embodiment does not install non-magnetic conductive materials: the upper damping disk 206 and the lower damping disk 207, and the effect achieved is: a smaller damping force is generated.
PUM
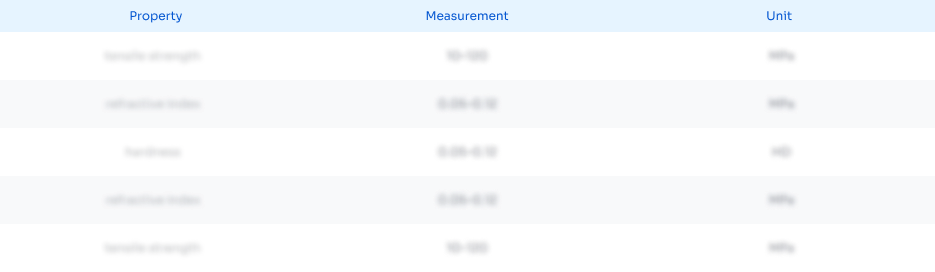
Abstract
Description
Claims
Application Information

- R&D
- Intellectual Property
- Life Sciences
- Materials
- Tech Scout
- Unparalleled Data Quality
- Higher Quality Content
- 60% Fewer Hallucinations
Browse by: Latest US Patents, China's latest patents, Technical Efficacy Thesaurus, Application Domain, Technology Topic, Popular Technical Reports.
© 2025 PatSnap. All rights reserved.Legal|Privacy policy|Modern Slavery Act Transparency Statement|Sitemap|About US| Contact US: help@patsnap.com