Manufacturing method of transformer coil
A technology of transformer coils and manufacturing methods, applied in the direction of inductance/transformer/magnet manufacturing, electrical components, circuits, etc., can solve the problem of winding different coil turns, and achieve the effect of improving multifunctionality
- Summary
- Abstract
- Description
- Claims
- Application Information
AI Technical Summary
Problems solved by technology
Method used
Image
Examples
Embodiment 1
[0047] see Figure 1-8 , is a schematic diagram of the overall structure of a method for manufacturing a transformer coil. A strip-shaped flat conductor is helically wound to form a helical structure, which includes the following steps:
[0048]S1), material preparation, preparing a flat conductor, and covering the surface of the flat conductor with paint to insulate the contact between two adjacent flat conductors;
[0049] S2), spiral winding, fixing one end of the flat conductor prepared in step S1 to the bottom of the inner mandrel; rotating the inner mandrel so that the flat conductor is wound around the inner mandrel to form a helical structure;
[0050] S3), tightness adjustment, when winding the flat conductor in step S2 on the inner mandrel, tighten the wound flat conductor to make the formed spiral structure more compact;
[0051] S4), the structure is shaped, and the flat conductor being wound in step S2 is compressed and shaped, so that the surface texture of the ...
Embodiment 2
[0064] see Figure 1-8 , is a schematic diagram of the overall structure of another transformer coil manufacturing method. This embodiment has similarities with Embodiment 1, and the similarities will not be described in this embodiment. The specific differences are:
[0065] A third sliding seat 402 is fixed on the bottom of the sidewall 4 , and the third sliding seat 402 is embedded in a third sliding groove 401 , and the third sliding groove 401 is arranged on the top of the chassis base 1 . The rib 4 is set to a square column structure, the top of the rib 4 is provided with a circular hole 407, and the bottom of the circular hole 407 is provided with a fixed seat 413; the side wall of the rib 4 is provided with a square hole 413, and the square hole 413 is connected with the circular hole 407 communicates, the hole wall of square hole 413 is symmetrically provided with the fourth chute 403, the side wall of circular hole 407 is provided with the 5th chute 405; Threaded rod...
PUM
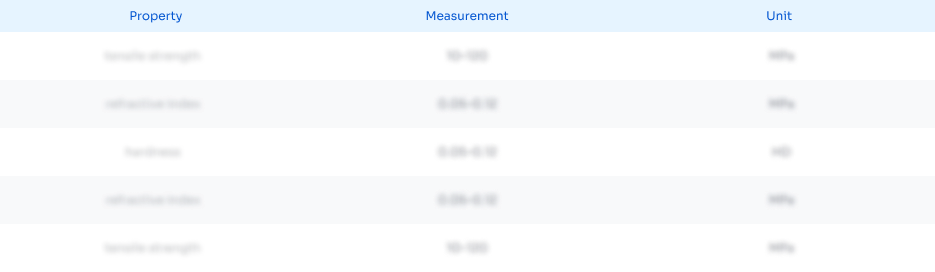
Abstract
Description
Claims
Application Information

- R&D
- Intellectual Property
- Life Sciences
- Materials
- Tech Scout
- Unparalleled Data Quality
- Higher Quality Content
- 60% Fewer Hallucinations
Browse by: Latest US Patents, China's latest patents, Technical Efficacy Thesaurus, Application Domain, Technology Topic, Popular Technical Reports.
© 2025 PatSnap. All rights reserved.Legal|Privacy policy|Modern Slavery Act Transparency Statement|Sitemap|About US| Contact US: help@patsnap.com