A preparation of cumn by vacuum induction melting 25 ni 10 alloy material method
A technology of vacuum induction melting and alloy materials, which is applied in the field of CuMn25Ni10 alloy materials, can solve the problems of patch resistance resistivity, unqualified temperature coefficient of resistance, large measurement errors and human errors, and high impurity content of alloy materials, so as to achieve convenient record analysis , Reduce element burning loss, less porosity effect
- Summary
- Abstract
- Description
- Claims
- Application Information
AI Technical Summary
Problems solved by technology
Method used
Image
Examples
Embodiment 1
[0034] CuMn 25 Ni 10 The preparation method of alloy material comprises the following steps:
[0035] (1) Preparation of CuNi 20 Master Alloy:
[0036] 1) Batching: take copper plate and nickel plate as raw materials with a weight percentage of 80%:20% for later use.
[0037] 2) Furnace vacuuming: Add copper and nickel plates into the clay crucible of the vacuum induction melting furnace by electrolysis, close the furnace cover, close the vent valve, and clean the observation window; open the mechanical pump and open the low vacuum baffle valve Vacuumize and turn on the Roots pump when the vacuum pressure in the furnace is ≤0.08MP.
[0038] 3) Melting: When the vacuum pressure in the furnace is less than or equal to 5Pa, the heating power is increased to 20KW and kept for 5 minutes; then the power is increased to 40KW and kept for 5 minutes; then the power is increased to 55KW and kept for 5 minutes; then the power is increased to 60KW and kept for 5 minutes; 5min; finall...
Embodiment 2
[0061] In order to solve the existing vacuum induction furnace's inability to accurately measure the real-time weight of castings and the discharge problem during the work of the vacuum induction furnace, the present invention designs a new furnace structure, the specific structure of which is as follows:
[0062] A down-casting vacuum induction furnace capable of accurately measuring casting weight, comprising a furnace body 1, the shape of the furnace body 1 is a hollow cylinder, a crucible 2 is arranged on the upper part of the inner cavity of the furnace body 1, and a furnace body 1 is arranged on the outer wall The inductor 3 corresponding to the position of the crucible 2 is provided with a copper mold 7 corresponding to the position of the crucible 2 under the inner cavity of the furnace body 1, and a copper mold 7 corresponding to the position of the copper mold 7 is arranged on the outer wall of the furnace body 1. Flat air extraction port 6; the copper mold 7 is place...
PUM
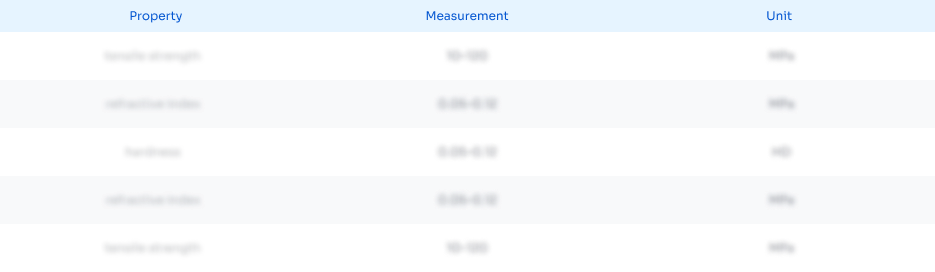
Abstract
Description
Claims
Application Information

- R&D
- Intellectual Property
- Life Sciences
- Materials
- Tech Scout
- Unparalleled Data Quality
- Higher Quality Content
- 60% Fewer Hallucinations
Browse by: Latest US Patents, China's latest patents, Technical Efficacy Thesaurus, Application Domain, Technology Topic, Popular Technical Reports.
© 2025 PatSnap. All rights reserved.Legal|Privacy policy|Modern Slavery Act Transparency Statement|Sitemap|About US| Contact US: help@patsnap.com