A material conveying and automatic loading and unloading system for main bearing cap processing
A technology of automatic loading and unloading and main bearing cap, which is applied in metal processing and other directions, can solve the problems of low manual loading and unloading efficiency, affecting processing efficiency, and high labor intensity, so as to improve processing production efficiency, reduce labor intensity, and improve The effect of work efficiency
- Summary
- Abstract
- Description
- Claims
- Application Information
AI Technical Summary
Problems solved by technology
Method used
Image
Examples
Embodiment Construction
[0038] The present invention will be further described in conjunction with the accompanying drawings and specific embodiments. It should be understood that these examples are only used to illustrate the present invention and are not intended to limit the scope of the present invention. In addition, it should be understood that after reading the content taught by the present invention, those skilled in the art may make various changes or modifications to the present invention, and these equivalent forms also fall within the scope defined in the present application.
[0039] Such as Figure 1-15 As shown, it is a material conveying and automatic loading and unloading system for the main bearing cap processing provided by the present invention, which is used for the automatic processing production line of the main bearing cap inner cold drilling equipment. In the present embodiment, workpiece 4 is 5309323 ( Figure 14 , Figure 15 Shown) the engine main bearing cap as an examp...
PUM
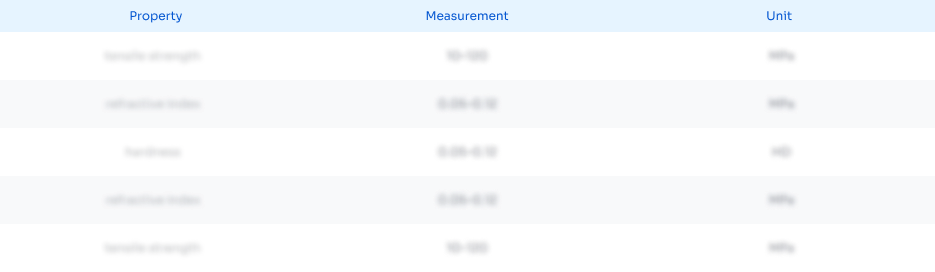
Abstract
Description
Claims
Application Information

- R&D
- Intellectual Property
- Life Sciences
- Materials
- Tech Scout
- Unparalleled Data Quality
- Higher Quality Content
- 60% Fewer Hallucinations
Browse by: Latest US Patents, China's latest patents, Technical Efficacy Thesaurus, Application Domain, Technology Topic, Popular Technical Reports.
© 2025 PatSnap. All rights reserved.Legal|Privacy policy|Modern Slavery Act Transparency Statement|Sitemap|About US| Contact US: help@patsnap.com