Production method of continuous hot-galvanized embossed plate
A production method and technology for embossed plates, which are applied in hot dip plating process, heat treatment furnace, heat treatment equipment, etc., can solve problems such as damage and peeling of surface protective film, production line speed and capacity restriction, poor adhesion of plate surface, etc. The effect of removing the machining process, increasing the productivity, and improving the weldability
- Summary
- Abstract
- Description
- Claims
- Application Information
AI Technical Summary
Problems solved by technology
Method used
Image
Examples
Embodiment 1
[0033]A method for producing continuous hot-dip galvanized on-line embossed sheets, comprising the following steps:
[0034] Step 1, Alkali washing and degreasing: Spray the hot lye with a temperature of 70°C on the strip surface after Kaiping, clean the oil, iron powder, dust and other attachments on the strip surface with a brush, and then use a temperature of 60 The hot water at ℃ washes the surface of the strip steel to remove the lye remaining on the surface of the strip steel to obtain a clean strip steel after degreasing. Stain residues to prevent the strip from being polluted and oxidized again after being wetted with water;
[0035] Step 2, annealing reduction: use the preheating section to rapidly heat the clean steel strip obtained in step 1 to below 700°C, and then fill the radiant tube section with 10% H 2 As a protective gas, reheat and soak the steel strip through the radiant tube section, the reheating temperature is 650°C, and the soaking temperature is 700°C...
PUM
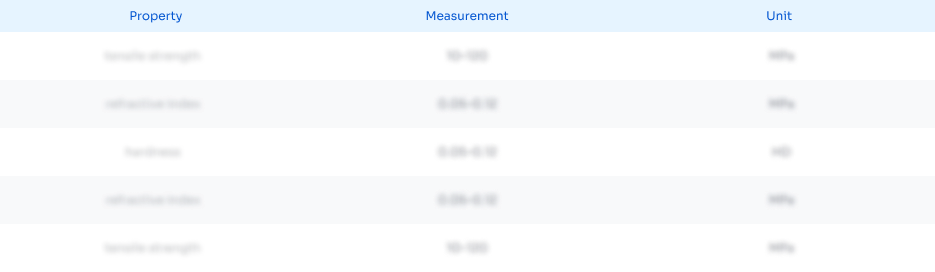
Abstract
Description
Claims
Application Information

- R&D
- Intellectual Property
- Life Sciences
- Materials
- Tech Scout
- Unparalleled Data Quality
- Higher Quality Content
- 60% Fewer Hallucinations
Browse by: Latest US Patents, China's latest patents, Technical Efficacy Thesaurus, Application Domain, Technology Topic, Popular Technical Reports.
© 2025 PatSnap. All rights reserved.Legal|Privacy policy|Modern Slavery Act Transparency Statement|Sitemap|About US| Contact US: help@patsnap.com