Preparation method of intelligent composite material containing delamination damage
A composite material and intelligent technology, applied in the field of materials, can solve the problems of indistinguishable damage signal and noise signal, X-ray damage to human body, complicated experimental procedures, etc. Effect
- Summary
- Abstract
- Description
- Claims
- Application Information
AI Technical Summary
Problems solved by technology
Method used
Image
Examples
Embodiment 1
[0030] Example 1, prepare a prefabricated 22-layer carbon fiber epoxy resin-based composite laminate test piece with a damage area of 10mm×10mm and a surface size of 200mm×25mm.
[0031] Step 1: Prepare before making
[0032] 1.1) Prepare the basic materials used:
[0033] Basic materials include: disinfectant, fiber cloth, PTFE film, fully transparent epoxy resin glue, fiber grating sensor, high temperature silicone, high temperature tape, flat mold, isolation film, air felt, vacuum bag and high temperature sealant;
[0034] 1.2) Prepare the equipment used:
[0035] Equipment includes: fiber cloth cutting machine, autoclave
[0036] 1.3) Scrub the work surface with a disinfectant to ensure the surface of the material is clean.
[0037] Step 2: Cut the fiber cloth.
[0038] The main technical material of the present invention is carbon fiber epoxy resin-based composite material fiber cloth. First, a whole piece of carbon fiber epoxy resin-based composite material fiber c...
Embodiment 2
[0062] Embodiment 2, the preparation of a prefabricated damage area is 15mm * 15mm, and the surface size of the test piece is a 22-layer carbon fiber epoxy resin-based composite laminate test piece of 200mm * 25mm;
[0063] Step 1: Preparation before making.
[0064] The specific implementation of this step is the same as Step 1 of Example 1.
[0065] Step 2: Cut the fiber cloth.
[0066] The specific implementation of this step is the same as step 2 of embodiment 1.
[0067] Step 3: Lay the optical fiber layer.
[0068] The specific implementation of this step is the same as step 3 of embodiment 1.
[0069] Step 4: Make a prefabricated damage layer.
[0070] In this embodiment, a polytetrafluoroethylene film with an area of 15 mm×15 mm is used as the prefabricated damaged layer of the test piece, and the remaining implementation methods are the same as Step 4 of Embodiment 1.
[0071] Step 5: Overall compounding.
[0072] The specific implementation of this step is th...
Embodiment 3
[0073] Embodiment 3, the preparation of a prefabricated damage area is 10mm * 10mm, and the surface size of the test piece is a 44-layer carbon fiber epoxy resin-based composite laminate test piece of 200mm * 25mm;
[0074] Step A: Preparation before making.
[0075] The specific implementation of this step is the same as Step 1 of Example 1.
[0076] Step B: cutting the fiber cloth.
[0077] In this example, 16 pieces of fiber cloth strips with a ply angle of 0°, 12 pieces of fiber cloth strips with a ply angle of 45°, 8 pieces of fiber cloth strips with a ply angle of -45°, and 8 pieces of fiber strips with a ply angle of 90° Cloth strips, all the other implementations are the same as step 2 of embodiment 1.
[0078] Step C: laying the optical fiber layer.
[0079] The specific implementation of this step is the same as step 3 of embodiment 1.
[0080] Step D: making a prefabricated damage layer.
[0081] The specific implementation of this step is the same as step 4 of...
PUM
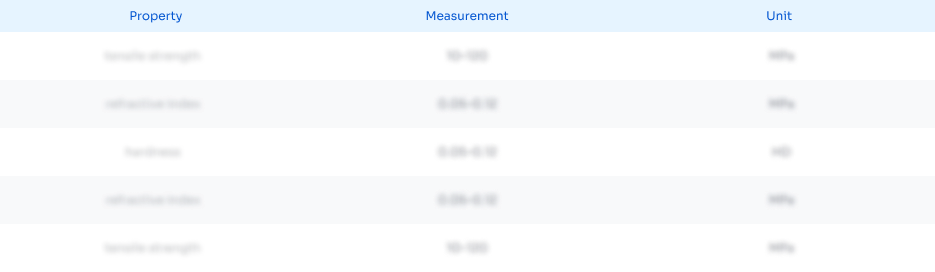
Abstract
Description
Claims
Application Information

- R&D Engineer
- R&D Manager
- IP Professional
- Industry Leading Data Capabilities
- Powerful AI technology
- Patent DNA Extraction
Browse by: Latest US Patents, China's latest patents, Technical Efficacy Thesaurus, Application Domain, Technology Topic, Popular Technical Reports.
© 2024 PatSnap. All rights reserved.Legal|Privacy policy|Modern Slavery Act Transparency Statement|Sitemap|About US| Contact US: help@patsnap.com