A structural thermal assessment test device with preload adjustment
A preload adjustment and test device technology, applied in the field of thermal assessment test, can solve the problems of heat leakage from the test piece to the surrounding tooling, unable to meet the assessment requirements, and the influence of the boundary effect is large, so as to achieve convenient application and eliminate the heating boundary effect. Impact, designability, and scalable effects
- Summary
- Abstract
- Description
- Claims
- Application Information
AI Technical Summary
Problems solved by technology
Method used
Image
Examples
Embodiment 1
[0037] Example 1 A thermal assessment test device for a heat insulation structure with preload adjustment
[0038] A heat insulation structure thermal assessment test device with pretightening force adjustment, the structure is left and right symmetrical, mainly including the precompression heat insulation structure to be assessed 6, deformation coordination plate 8, heating element 9, loading device 10, and pretightening force pressing plate 11. Install the adjustment structure 12, the pressure sensor 13, the bearing structure 2, etc., such as image 3 shown.
[0039] The two deformation coordinating plates 8 are symmetrically arranged on the left and right, the loading device 10 is installed on the same end of the two deformation coordinating plates 8 for fixing, and the heating element 9 is arranged in the middle of the two deformation coordinating plates 8; the outer sides of the two deformation coordinating plates 8 are arranged in sequence The pre-compressed heat insulati...
Embodiment 2
[0044] Example 2 Thermal assessment test of heat-sealed structure with pre-tightening adjustment
[0045] A thermal assessment test device for a heat-sealed structure with pre-tightening force adjustment, mainly including a pre-compression heat-sealed structure to be assessed 1, a deformation coordination plate 8, a heating element 9, a loading device 10, a pre-tightening force pressing plate 11, and an installation adjustment Structure 12, pressure sensor 13, bearing structure 2, auxiliary heat insulation structure 14, heat insulation pressure plate 15, temperature control sensor 16, such as Figure 4 As shown, the relative positions of the deformation coordinating plate 8, the loading device 10, the pre-tightening force pressing plate 11, the installation adjustment structure 12, and the pressure sensor 13 are basically the same as those in Embodiment 1, except that the deformation coordinating plate 8, the pre-tightening force applying pressure Other components vary between...
PUM
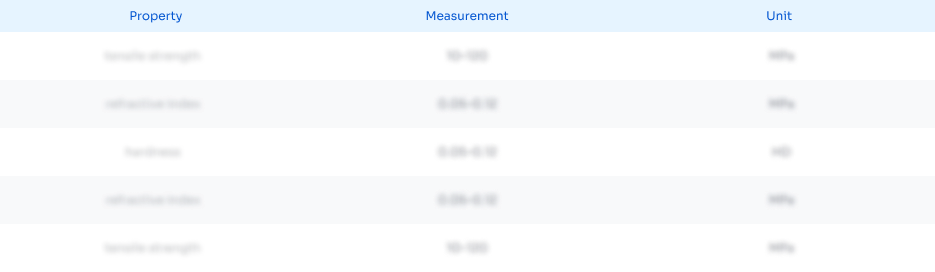
Abstract
Description
Claims
Application Information

- R&D
- Intellectual Property
- Life Sciences
- Materials
- Tech Scout
- Unparalleled Data Quality
- Higher Quality Content
- 60% Fewer Hallucinations
Browse by: Latest US Patents, China's latest patents, Technical Efficacy Thesaurus, Application Domain, Technology Topic, Popular Technical Reports.
© 2025 PatSnap. All rights reserved.Legal|Privacy policy|Modern Slavery Act Transparency Statement|Sitemap|About US| Contact US: help@patsnap.com