Screw extruder and method for regenerating rubber by adopting screw extruder
A technology of screw extruder and recycled rubber, which is applied in the field of screw extruder and recycled rubber using screw extruder, which can solve the problems of low heating efficiency and poor performance of extruded materials
- Summary
- Abstract
- Description
- Claims
- Application Information
AI Technical Summary
Problems solved by technology
Method used
Image
Examples
Embodiment 1
[0060] Such as figure 1 As shown, the screw extruder of this embodiment includes a screw extruder main body 1 and a barrel 200, the base end of the barrel 200 is fixed to the screw extruder main body 1, and the barrel 200 consists of a plurality of barrel blocks 2 along a The directions are connected to each other, and the barrel 200 is divided into a heating section 201, a reaction section 202 and a cooling section 203 along the extrusion direction of the material in the screw extruder.
[0061] Such as image 3 As shown, the cylinder block 2 constituting the barrel 200 is a cuboid block structure, more specifically, the cylinder block 2 has a first end surface 22a and a second end surface 22b arranged oppositely and four connecting first end surfaces and the second end surfaces. On the side, the first end surface 22a and the second end surface 22b have the same shape. Further, the edge portions of the first end surface 22a and the second end surface 22b protrude outward to ...
Embodiment 2
[0073] A method for regenerating rubber using the screw extruder of Embodiment 1. First, start the heating rod 30 to preheat the material cylinder 20 in the barrel 200 to raise the temperature. 85 minutes, finally preheating the temperature of material vat 20 to 100-150°C, and preheating the temperature of material vat 20 slowly through heating rod 30 to ensure that the temperature in material vat 20 is uniform, which is beneficial to the performance of the product when the material is extruded. At the same time, The slow temperature rise avoids the influence of the structure of the barrel block 2 and the screw structure by the temperature, and prolongs the effective service life of the screw extruder; after the preheating is completed, start the screw extruder, and add waste rubber and regenerant into the material tank 20, Among them, the regenerant is a mixture of coumarone resin and pine tar in a mass ratio of 3:7, and the mass ratio of waste rubber to regenerant is 100:15; ...
PUM
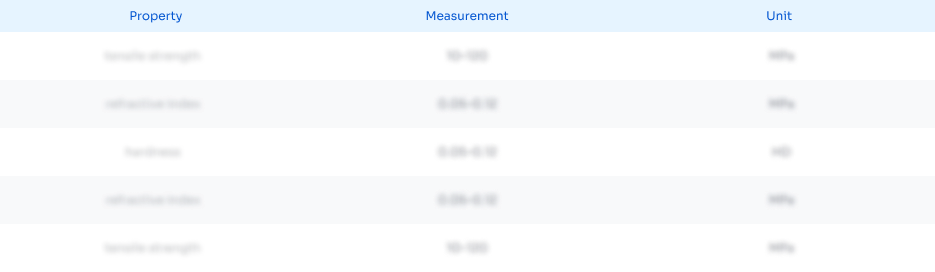
Abstract
Description
Claims
Application Information

- R&D
- Intellectual Property
- Life Sciences
- Materials
- Tech Scout
- Unparalleled Data Quality
- Higher Quality Content
- 60% Fewer Hallucinations
Browse by: Latest US Patents, China's latest patents, Technical Efficacy Thesaurus, Application Domain, Technology Topic, Popular Technical Reports.
© 2025 PatSnap. All rights reserved.Legal|Privacy policy|Modern Slavery Act Transparency Statement|Sitemap|About US| Contact US: help@patsnap.com