Dissolving device for production of liquid sodium silicate
A technology of liquid sodium silicate and cylinder, applied in the direction of feeding device, silicate, alkali metal silicate, etc., can solve the problems of increasing feeding time, increasing the time of materialization, steam consumption, difficult operation, etc., to achieve Improve product output and quality, reduce steam consumption, and achieve uniform liquid concentration
- Summary
- Abstract
- Description
- Claims
- Application Information
AI Technical Summary
Problems solved by technology
Method used
Image
Examples
Embodiment 1
[0043] Such as figure 1 As shown, this embodiment introduces a chemical material device for the production of liquid sodium silicate, which is used for static chemical material, and includes a cylinder 1 whose axis extends horizontally. That is, the cylinder body 1 is a horizontal cylinder body.
[0044]The chemical material device of the present invention is essentially a horizontal chemical material tank. The horizontal chemical material tank has low cost and takes up little space. The horizontal chemical material tank can be installed in the workshop, and liquid The sodium silicate filter platform makes full use of space advantages; it reduces the cost of installing insulation on the outer wall of the kettle. The horizontal feed tank of the present invention is only about 3 meters away from the ground at the feeding port 4, which reduces the transport distance of the solid sodium silicate block, accelerates the feeding speed, and reduces the feeding time. The grate 7 of t...
Embodiment 2
[0048] Such as Figure 1-3 As shown, the difference between this embodiment and Embodiment 1 is that there is at least one feeding port 4 on the top of the cylinder body 1, and the cylinder body 1 on the side of the feeding port 4 is provided with a water filling port 2, a pressure gauge 15, an emptying port 5, and a safety valve. A valve 19, a manhole 3 and at least one sampling port 6 are provided on the side of the cylinder body 1, and at least one drain port 11 is provided at the bottom of the cylinder body 1. Manhole 3 is arranged higher than grate 7.
[0049] Specifically, the feeding port 4, the water feeding port 2, the pressure gauge 15, the emptying port 5, the safety valve 19, the cleaning port 11 and the manhole 3 are all arranged on the straight cylinder, and the sampling port 6 is arranged on the cover.
[0050] Preferably, a feeding port 4 is respectively provided on both sides of the top of the cylinder body 1 .
[0051] The horizontal chemical feed kettle of...
Embodiment 3
[0056] Such as Figure 1-5 As shown, the difference between this embodiment and Embodiments 1 to 2 is that a horizontally arranged grate 7 and a steam pipe 10 arranged below the grate 7 are arranged inside the cylinder body 1, and the steam pipe 10 is arranged parallel to the grate 7. A plurality of steam outlet holes 20 are distributed on the pipe wall.
[0057] The steam pipeline 10 of the above structure is convenient for laying, which reduces the difficulty of implementation, and the horizontal chemical tank of the present invention can install more steam pipelines 10 inside. It needs 2 pressurization and 1 depressurization to complete the solid sodium silicate material, thus reducing the steam consumption.
[0058] A steam inlet 17 arranged lower than the grate 7 is provided on the side of the cylinder body 1 , and the steam inlet end of the steam pipe 10 protrudes from the steam inlet 17 to the outside of the cylinder body 1 . The steam inlet 17 is located on the cover...
PUM
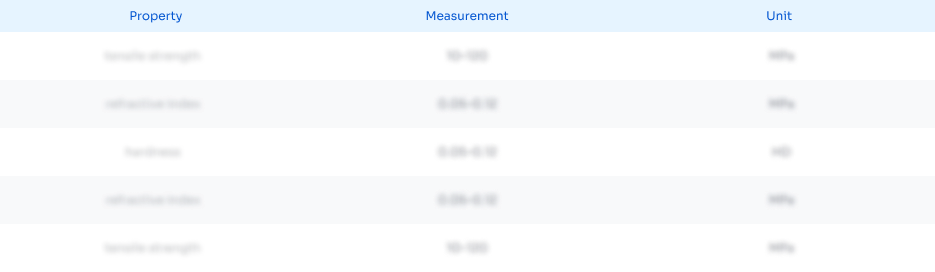
Abstract
Description
Claims
Application Information

- Generate Ideas
- Intellectual Property
- Life Sciences
- Materials
- Tech Scout
- Unparalleled Data Quality
- Higher Quality Content
- 60% Fewer Hallucinations
Browse by: Latest US Patents, China's latest patents, Technical Efficacy Thesaurus, Application Domain, Technology Topic, Popular Technical Reports.
© 2025 PatSnap. All rights reserved.Legal|Privacy policy|Modern Slavery Act Transparency Statement|Sitemap|About US| Contact US: help@patsnap.com