Hexahedral mesh division complex pattern tire finite element modeling method
A complex pattern and mesh division technology, applied in the field of tire finite element modeling, can solve the problems of complex modeling and inaccurate finite element models, and achieve the effects of accurate finite element models, reducing binding contact, and improving efficiency
- Summary
- Abstract
- Description
- Claims
- Application Information
AI Technical Summary
Problems solved by technology
Method used
Image
Examples
Embodiment Construction
[0031] The specific implementation of the present invention will be further described below in conjunction with the accompanying drawings, which are only preferred embodiments of the present invention, but the implementation and protection scope of the invention are not limited thereto.
[0032] Taking a certain type of off-road vehicle pattern tire as an example, a finite element modeling method for complex pattern tires divided by hexahedral meshes includes steps:
[0033] S1. Draw the two-dimensional cross-sectional geometric model of the tire, carry out the tire segmentation process in advance according to the characteristics of the tread block, and write down the total number of segments N, which is 46 in this embodiment;
[0034] S2. Set the coordinate points of the key geometric features of the tread pattern block, and project the geometric feature points of a segment of the pattern block to a two-dimensional plane grid through segmental expression;
[0035] S3. Project...
PUM
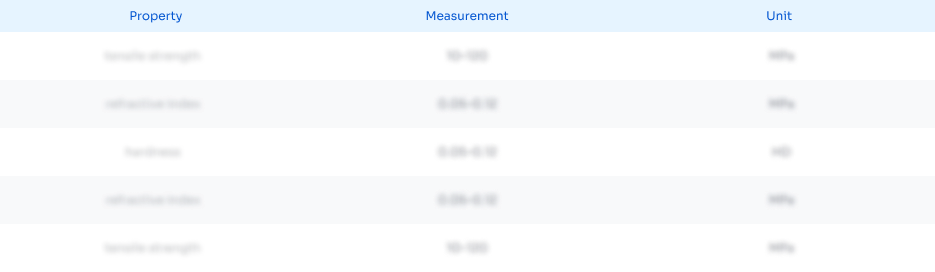
Abstract
Description
Claims
Application Information

- R&D
- Intellectual Property
- Life Sciences
- Materials
- Tech Scout
- Unparalleled Data Quality
- Higher Quality Content
- 60% Fewer Hallucinations
Browse by: Latest US Patents, China's latest patents, Technical Efficacy Thesaurus, Application Domain, Technology Topic, Popular Technical Reports.
© 2025 PatSnap. All rights reserved.Legal|Privacy policy|Modern Slavery Act Transparency Statement|Sitemap|About US| Contact US: help@patsnap.com