Steel strip surface roll coating machine
A technology of roller coater and steel strip, which is applied in the field of roller coater frame and steel strip surface roller coating equipment, which can solve the problem of motor blockage of coating roller, precise reduction of film thickness, inability to adjust and control the pressure between rollers on one side, etc. problems, to achieve the effect of improving uniformity and accuracy, direct detection by roller pressure, and eliminating film thickness defects
- Summary
- Abstract
- Description
- Claims
- Application Information
AI Technical Summary
Problems solved by technology
Method used
Image
Examples
Embodiment
[0037] The placement of rolling mill transmission motors and other equipment in the steel rolling production line needs to be uniformly designed. The side close to the operation table is called the operation side, and the side where the transmission device is located is called the transmission side. Both ends of the coating roller 2 and the liquid-taking roller 3 are respectively supported on the bearing housing 25 through bearings, and the extension shafts of the coating roller 2 and the liquid-taking roller 3 at the transmission side are connected with the driving motor. The extension shafts of the coating roller 2 and the liquid-taking roller 3 located at the drive side are respectively connected with the drive motor through telescopic ball cages.
[0038] Such as Figure 5 As shown, the bearings on the coating roller 2 and the liquid-taking roller 3 at the drive side are all self-aligning floating bearings 26, and the bearings on the coating roller 2 and the liquid-takin...
PUM
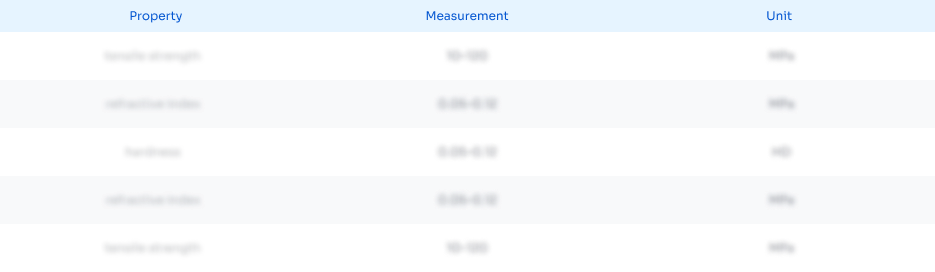
Abstract
Description
Claims
Application Information

- Generate Ideas
- Intellectual Property
- Life Sciences
- Materials
- Tech Scout
- Unparalleled Data Quality
- Higher Quality Content
- 60% Fewer Hallucinations
Browse by: Latest US Patents, China's latest patents, Technical Efficacy Thesaurus, Application Domain, Technology Topic, Popular Technical Reports.
© 2025 PatSnap. All rights reserved.Legal|Privacy policy|Modern Slavery Act Transparency Statement|Sitemap|About US| Contact US: help@patsnap.com