A vanadium pentoxide integrated drying, deammonification and oxidation melting tablet making system
A vanadium pentoxide, oxidative melting technology, applied in vanadium oxide and other directions, can solve the problems of inability to realize continuous feeding and discharging, waste of environmental pollution, aggravate energy, etc., to solve the difficulty of waste water and waste gas treatment, and reduce environmental pollution. , to avoid the effect of the reduction reaction
- Summary
- Abstract
- Description
- Claims
- Application Information
AI Technical Summary
Problems solved by technology
Method used
Image
Examples
Embodiment Construction
[0042] The following will clearly and completely describe the technical solutions in the embodiments of the present invention with reference to the drawings in the embodiments of the present invention. Apparently, the described embodiments are only some of the embodiments of the present invention, but not all of them. Based on the embodiments of the present invention, all other embodiments obtained by persons of ordinary skill in the art without making creative efforts belong to the protection scope of the present invention.
[0043] Such as Figure 1-4 As shown, a vanadium pentoxide integrated drying, deammonification and oxidative melting film making system includes a drum dryer 1, a spray evaporator 2, a steam condensing device 3 and a melting furnace 4, and one side of the drum dryer 1 A screw feeder 5 is connected, and a silo 6 is arranged above the screw feeder 5. The top outlet of the drum dryer 1 is connected to the melting furnace 4 through the feeding pipeline 7 and...
PUM
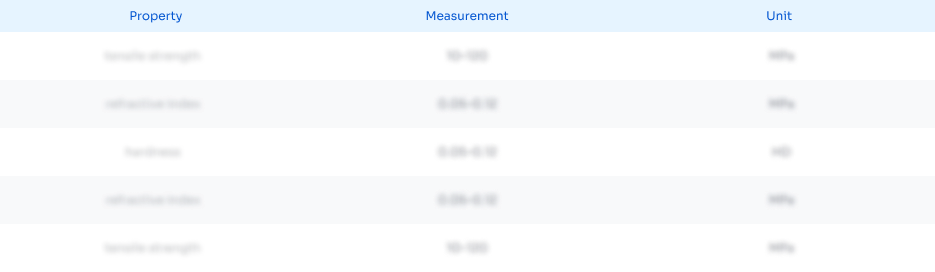
Abstract
Description
Claims
Application Information

- Generate Ideas
- Intellectual Property
- Life Sciences
- Materials
- Tech Scout
- Unparalleled Data Quality
- Higher Quality Content
- 60% Fewer Hallucinations
Browse by: Latest US Patents, China's latest patents, Technical Efficacy Thesaurus, Application Domain, Technology Topic, Popular Technical Reports.
© 2025 PatSnap. All rights reserved.Legal|Privacy policy|Modern Slavery Act Transparency Statement|Sitemap|About US| Contact US: help@patsnap.com