Lithium battery laminating machine
A compound machine and lithium battery technology, which is applied in the direction of non-aqueous electrolyte battery, electrolyte battery manufacturing, sustainable manufacturing/processing, etc., can solve the problems of safety hazards, low production efficiency, etc., to improve production efficiency and reduce manual work time Effect
- Summary
- Abstract
- Description
- Claims
- Application Information
AI Technical Summary
Problems solved by technology
Method used
Image
Examples
Embodiment 1
[0045] Such as Figure 1-7 As shown, this embodiment provides a lithium battery composite machine, which includes a feeding device 10 for inputting the diaphragm and the pole piece, and is used for stacking the pole piece and the diaphragm so that the pole piece and the diaphragm form a composite and The driving device 20 for transporting the composite, the heating device 30 for heating the composite to a preset high temperature, and the extrusion of the composite heated to a high temperature by the heating device 30 to make the pole piece and the separator at high temperature adhere A synthetic pressing device 40, and a cutting device 50 for cutting the formed composite to a preset length, the output end of the feeding device 10 is connected to the input end of the driving device 20, and the heating device 30 and the pressing device 40 are all arranged on the moving stroke of the composite body driven by the driving device 20, the heating device 30 and the pressing device 40 ...
Embodiment 2
[0060] Such as figure 2 As shown, the feeding device 10 in this embodiment also includes a pair of roller drive mechanism 15, two groups of the third material roller 13, the first material roller 11, the pair of roller drive mechanism 15 and the second material roller. Rollers 12 are all arranged on one side of the first guide port, and the pair of roller driving mechanisms 15 are arranged between the third material roller 13 and the second material roller 12, and the pair of roller driving mechanisms 15 are used for To pre-compress the pole piece and the diaphragm conveyed by the second material roller 12 and the third material roller 13, so as to prevent the pole piece and the pole piece overlapped by the corresponding pole piece and the diaphragm from being guided through the first guide port The thickness of the complex composed of the diaphragm is too large to block the first guide port.
[0061] In this embodiment, the pair of roller driving mechanisms 15 includes a fo...
Embodiment 3
[0073] Such as image 3 As shown, the driving device 20 in this embodiment includes a fourth material roller 21, a fifth material roller 22, a sixth material roller 23, a seventh material roller 24, a first synchronous wheel assembly 20C, a second synchronous wheel assembly 20D, The third synchronous wheel assembly 20E, the fourth synchronous wheel assembly 20F, the first drive member (not marked in the drawings), the second drive member (not marked in the drawings) and the first drive motor (not marked in the figures), the first The fourth material roller 21 and the fifth material roller 22 are arranged symmetrically up and down, the sixth material roller 23 and the seventh material roller 24 are arranged symmetrically up and down, and the first synchronous wheel assembly 20C and the second synchronous wheel assembly 20C The synchronous wheel assembly 20D is arranged symmetrically up and down, the third synchronous wheel assembly 20E and the fourth synchronous wheel assembly ...
PUM
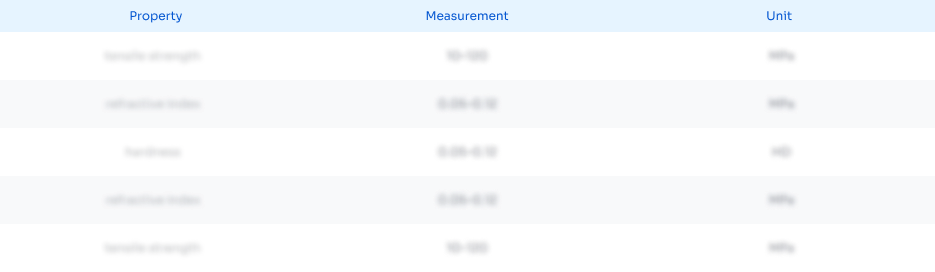
Abstract
Description
Claims
Application Information

- R&D
- Intellectual Property
- Life Sciences
- Materials
- Tech Scout
- Unparalleled Data Quality
- Higher Quality Content
- 60% Fewer Hallucinations
Browse by: Latest US Patents, China's latest patents, Technical Efficacy Thesaurus, Application Domain, Technology Topic, Popular Technical Reports.
© 2025 PatSnap. All rights reserved.Legal|Privacy policy|Modern Slavery Act Transparency Statement|Sitemap|About US| Contact US: help@patsnap.com