Covering rheological agent and preparation method thereof
A rheological agent and hiding technology, applied in the direction of pigmented coatings, coatings, paper coatings, etc., can solve the problems of poor water retention, low hiding, and poor rheological properties of paper coatings, so as to improve water retention and avoid Flocculation and precipitation, enhance the effect of stress resistance
- Summary
- Abstract
- Description
- Claims
- Application Information
AI Technical Summary
Problems solved by technology
Method used
Image
Examples
Embodiment 1
[0041] The opacifying rheological agent provided by the present embodiment has a preparation method as follows:
[0042] Add 60 parts of deionized water, 5 parts of cationic monomer dimethyl diallyl ammonium chloride, 1 part of anionic monomer acrylic acid, 30 parts of hard monomer styrene, 2 parts of crosslinking monomer methyl Hydroxyethyl acrylate, 0.2 part of chain transfer agent mercaptoethanol, 0.4 part of nonionic surfactant alkylphenol polyoxyethylene ether, 0.1 part of reducing agent sodium sulfite, 0.8 part of pH buffer agent sodium bicarbonate, start stirring and mixing evenly, and heat to 60°C, keep warm for 10-20 minutes;
[0043] Increase the stirring speed, and raise the temperature to 90°C, and keep it warm for 10-20 minutes;
[0044]Reduce the stirring speed, add 25% of the total amount of initiator (0.2 parts of ammonium persulfate and potassium persulfate 1:1 mixture) (that is, 0.05 parts of ammonium persulfate and potassium persulfate 1:1 mixture), start t...
Embodiment 2
[0050] Add 60 parts of deionized water, 6 parts of cationic monomer dimethyl diallyl ammonium chloride, 1 part of anionic monomer acrylic acid, 28 parts of hard monomer styrene, 3 parts of crosslinking monomer methyl Hydroxyethyl acrylate, 0.2 part of chain transfer agent mercaptoethanol, 0.6 part of nonionic surfactant alkylphenol polyoxyethylene ether, 0.1 part of reducing agent sodium sulfite, 0.6 part of pH buffer agent sodium bicarbonate, start stirring and mixing evenly, and heat to 60°C, keep warm for 10-20 minutes;
[0051] Increase the stirring speed, and raise the temperature to 90°C, and keep it warm for 10-20 minutes;
[0052] Reduce the stirring speed, add 25% of the total amount of initiator (0.2 parts of ammonium persulfate and potassium persulfate 1:1 mixture) (that is, 0.05 parts of ammonium persulfate and potassium persulfate 1:1 mixture), start the reaction and keep the temperature stable;
[0053] After reacting for 60 minutes, add 25% of the total amount ...
Embodiment 3
[0058] Add 60 parts of deionized water, 8 parts of cationic monomer dimethyl diallyl ammonium chloride, 0.5 parts of anionic monomer acrylic acid, 25 parts of hard monomer styrene, 4 parts of crosslinking monomer methyl Hydroxyethyl acrylate, 0.4 part of chain transfer agent mercaptoethanol, 0.7 part of nonionic surfactant alkylphenol polyoxyethylene ether, 0.1 part of reducing agent sodium sulfite, 0.7 part of pH buffer agent sodium bicarbonate, start stirring and mixing evenly, and heat to 60°C, keep warm for 10-20 minutes;
[0059] Increase the stirring speed, and raise the temperature to 90°C, and keep it warm for 10-20 minutes;
[0060] Reduce the stirring speed, add 25% (ie 0.075 parts of ammonium persulfate and potassium persulfate 1:1 mixture) of the total amount of initiator (0.3 parts of ammonium persulfate and potassium persulfate 1:1 mixture), start the reaction and keep the temperature stable;
[0061] After reacting for 60 minutes, add 25% of the total amount of...
PUM
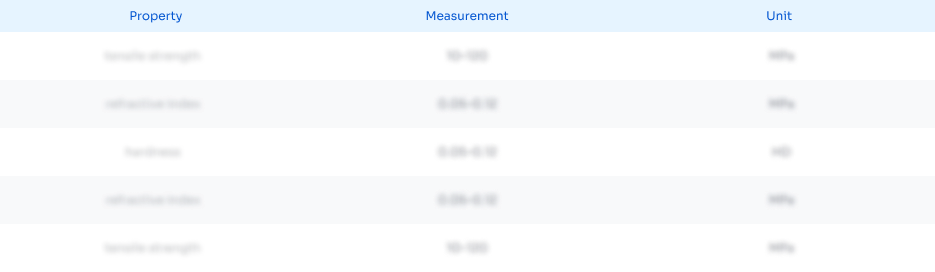
Abstract
Description
Claims
Application Information

- Generate Ideas
- Intellectual Property
- Life Sciences
- Materials
- Tech Scout
- Unparalleled Data Quality
- Higher Quality Content
- 60% Fewer Hallucinations
Browse by: Latest US Patents, China's latest patents, Technical Efficacy Thesaurus, Application Domain, Technology Topic, Popular Technical Reports.
© 2025 PatSnap. All rights reserved.Legal|Privacy policy|Modern Slavery Act Transparency Statement|Sitemap|About US| Contact US: help@patsnap.com