External clamping-type sensor parameterized installation method
A technology of sensor parameters and installation methods, which is applied in the direction of instruments, measuring devices, liquid/fluid solid measurement, etc., can solve problems such as installation errors and lacks, reduce system errors, simplify device principles, and improve operating efficiency Effect
- Summary
- Abstract
- Description
- Claims
- Application Information
AI Technical Summary
Problems solved by technology
Method used
Image
Examples
Embodiment 1
[0037] The implementation process of the parameterized installation method of the external clip-on sensor in this embodiment is as follows figure 1 As shown, the detailed steps are as follows:
[0038] Step 1: Initial State Calibration
[0039] When the inner surface of the interface B end 52 is located at the axial position of the measured pipeline 1 , it is the initial state of the radial screw 23 , and at this time, the reading of the radial scale 24 is 0. When the movable frame 22 is close to the fixed frame 21, it is the initial state of the axial scale 31, at this time, the reading of the axial scale 31 is 0, assembled on the installation interface 5 The two external clip-on sensors 4, their opposite end faces are in the same plane, and the projection distance of the center point of the sensing area along the axial direction of the measured pipeline 1 is recorded as L0 .
[0040] Step 2: Determine the radial scale 24 target scale
[0041] The outer wall radius of th...
Embodiment 2
[0055] In this embodiment, a reflection method is used for measurement, and the V method is used to install the sensor. It is assumed that the inner wall radius of a certain pipeline 1 r 70mm, outer wall radius R According to the measurement technical requirements of the ultrasonic flowmeter, the installation distance of the two external clip-on sensors 4 is calculated l It is 100mm (here is a hypothetical value, which is only used for the description of the embodiment of the present invention), and the V method is used for installation, and a small-sized fixing device can be used. Measured by calibration experiments L 0 is 20mm, the projected width of the clamp-on sensor 4 in the radial direction of the measured pipeline 1 d is 30mm.
[0056] The installation parameters calculated by formulas 1~3 are: D 1 =R+d=105mm, D 2 =R=75mm, L=l-L 0 = 80mm .
[0057] One of the radial screw rods 23 on the fixed frame 21 and the movable frame 22 is respectively selected f...
Embodiment 3
[0061] In this embodiment, the direct transmission method is used for measurement, and the Z method is used to install the sensor. It is assumed that the inner wall radius of a certain pipeline 1 r 260mm, outer wall radius R is 270mm, according to the measurement technical requirements of ultrasonic flowmeter, the installation distance of two external clip-on sensors 4 is calculated l It is 240mm (here is a hypothetical value, which is only used for the description of the embodiment of the present invention), and it is installed by Z method, and a medium-sized fixing device can be used. Measured by calibration experiments L 0 is 20mm, the projected width of the clamp-on sensor 4 in the radial direction of the measured pipeline 1 d is 30mm.
[0062] The installation parameters calculated by formulas 1~3 are: D 1 =R+d=300mm, D 2 =R=270mm, L=l-L 0 = 220mm.
[0063] One of the radial screw rods 23 on the fixed frame 21 and the movable frame 22 is respectively selec...
PUM
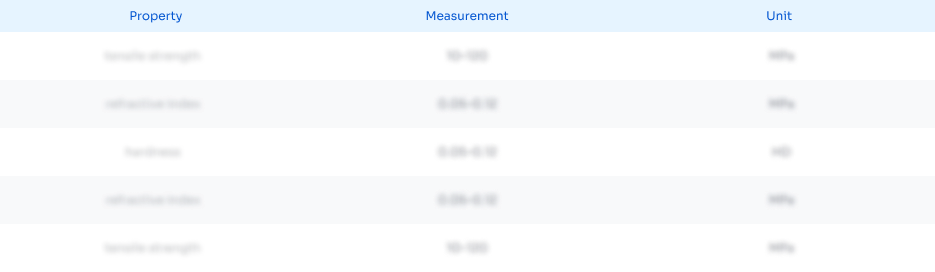
Abstract
Description
Claims
Application Information

- R&D
- Intellectual Property
- Life Sciences
- Materials
- Tech Scout
- Unparalleled Data Quality
- Higher Quality Content
- 60% Fewer Hallucinations
Browse by: Latest US Patents, China's latest patents, Technical Efficacy Thesaurus, Application Domain, Technology Topic, Popular Technical Reports.
© 2025 PatSnap. All rights reserved.Legal|Privacy policy|Modern Slavery Act Transparency Statement|Sitemap|About US| Contact US: help@patsnap.com