Plastic particle production system
A production system and technology for plastic granules, applied in the field of plastic granule production equipment, can solve problems such as uneven size of plastic strips
- Summary
- Abstract
- Description
- Claims
- Application Information
AI Technical Summary
Problems solved by technology
Method used
Image
Examples
Embodiment 1
[0028] Embodiment 1 is basically as follows:
[0029] Plastic pellet production systems such as figure 1 As shown, an extruder is included, and the extruder includes a housing 10, a screw 12 and a die 20, the left end of the housing 10 is provided with a feed hopper 11, and the inner wall of the housing 10 is provided with an electric heating wire for heating the raw materials to form a molten state . The screw 12 is located within the housing 10 . An extruding motor is fixed outside the housing 10 , and the power shaft of the extruding motor passes through the housing 10 and is fixed with the screw rod 12 . The screw 12 rotates under the drive of the extrusion motor to stir the raw materials and transport them to the right.
[0030] The right end of the screw rod 12 is a discharge end, and an intermittent discharge mechanism is provided outside the discharge end. The intermittent discharge mechanism includes a control plate 13 and a baffle plate 14. The control plate 13 an...
Embodiment 2
[0035] The difference from Embodiment 1 is that, as Figure 5 As shown, a cooling pipe 30 is provided below the cutting knife 23 , and a receiving hopper 31 is provided on the cooling pipe 30 . The receiving hopper 31 can catch the cut plastic particles and the cooling water flowing out from the rapid cooling chamber 22 and enter the cooling pipe 30 . In order to further cool the plastic particles, the left end of the cooling pipe 30 is also connected with a water supply pipe 21, and a cooling motor is fixed outside the left end of the cooling pipe 30, and the output shaft of the cooling motor extends into the cooling pipe 30 and is connected with an impeller. Driven by the cooling motor, the impeller transports the cooling water supplied by the water supply pipe 21 to the right, and mixes with the plastic particles to further cool the plastic particles. In order to enable the plastic particles to roll repeatedly in the cooling pipe 30 to accelerate cooling, a helical baffle ...
PUM
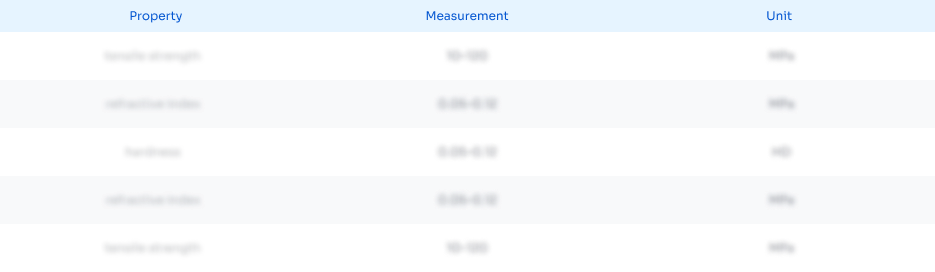
Abstract
Description
Claims
Application Information

- R&D Engineer
- R&D Manager
- IP Professional
- Industry Leading Data Capabilities
- Powerful AI technology
- Patent DNA Extraction
Browse by: Latest US Patents, China's latest patents, Technical Efficacy Thesaurus, Application Domain, Technology Topic, Popular Technical Reports.
© 2024 PatSnap. All rights reserved.Legal|Privacy policy|Modern Slavery Act Transparency Statement|Sitemap|About US| Contact US: help@patsnap.com