Rolling bearing fault feature extraction method based on CEEMD and FastICA
A technology of fault characteristics and extraction methods, applied in the testing of mechanical components, testing of machine/structural components, measuring devices, etc.
- Summary
- Abstract
- Description
- Claims
- Application Information
AI Technical Summary
Problems solved by technology
Method used
Image
Examples
Embodiment 1
[0070] Embodiment 1: as figure 1 As shown, a rolling bearing fault feature extraction method based on CEEMD and FastICA, first uses the CEEMD algorithm to decompose the original fault vibration signal x(t) into several IMF components of different frequencies, and then selects the corresponding IMF components according to the kurtosis criterion for reconstruction Get the observed signal G 1 (t), the remaining IMF components are reconstructed to obtain the virtual noise channel signal G 2 (t); use the FastICA algorithm to convert the observed signal G 1 (t) and virtual noise channel signal G 2 (t) Perform unmixing and denoising processing to obtain the signal Z(t) after joint noise reduction; then use the Teager energy operator to demodulate the signal Z(t) after joint noise reduction to obtain the demodulated signal W(n) ; Finally, perform FFT transformation on the demodulated signal W(n), analyze the spectral characteristics of the transformed signal Y(t), extract the fault...
Embodiment 2
[0077] Embodiment 2: In this embodiment, the fault signal of the outer ring of the rolling bearing is analyzed, and the fault signal of the inner ring of the bearing is decomposed by CEEMD to several IMF components; the kurtosis value of each IMF component signal is calculated separately, and the kurtosis value is selected to be larger The first two component signals are reconstructed to obtain the observed signal, and the remaining IMF components construct the virtual noise channel signal; the observed signal and the virtual channel signal are unmixed using the FastICA algorithm to obtain the joint noise-reduced signal; the noise-reduced The signal is demodulated by the Teager-Kaiser energy operator to obtain the demodulated signal; FFT is performed on the demodulated signal to obtain the signal spectrum as shown in Figure 7 shown by Figure 7 It can be clearly obtained that the fundamental frequency of the inner ring fault of the rolling bearing is 105.5 Hz (close to the op...
PUM
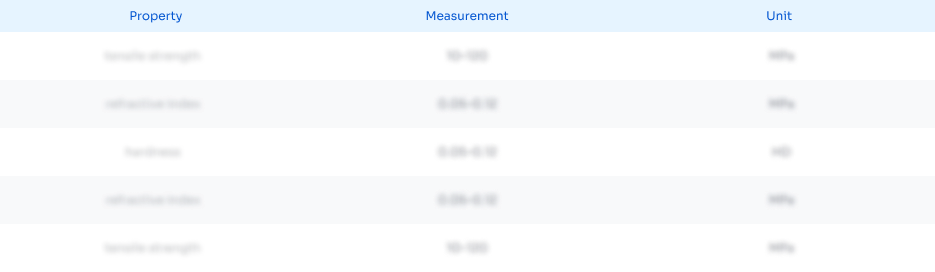
Abstract
Description
Claims
Application Information

- R&D
- Intellectual Property
- Life Sciences
- Materials
- Tech Scout
- Unparalleled Data Quality
- Higher Quality Content
- 60% Fewer Hallucinations
Browse by: Latest US Patents, China's latest patents, Technical Efficacy Thesaurus, Application Domain, Technology Topic, Popular Technical Reports.
© 2025 PatSnap. All rights reserved.Legal|Privacy policy|Modern Slavery Act Transparency Statement|Sitemap|About US| Contact US: help@patsnap.com