Methods to prevent the explosion of electrostatic precipitators
An electrostatic precipitator and explosion venting technology, which is applied in the manufacture of converters, etc., can solve the problems of electrostatic precipitator explosion venting, and achieve the effect of avoiding explosion venting and energy-saving operation
- Summary
- Abstract
- Description
- Claims
- Application Information
AI Technical Summary
Problems solved by technology
Method used
Examples
Embodiment 1
[0028] Electrostatic precipitator position: Set the preset outlet temperature of the evaporative cooler to 260°C. In the first 16s before blowing, the water regulating valve of the evaporative cooler is controlled by a fixed opening, and the opening is controlled at 18%. The flow rate of the evaporative cooler 20Nm 3 / h, 16s after the start of blowing, the water distribution regulating valve of the evaporative cooler automatically adjusts the water distribution through the PID control system according to the actual outlet temperature and the preset outlet temperature of the evaporative cooler, and the P and I control parameters are set to 1.0 and 0.8 respectively.
[0029] Converter post: After blowing starts, the post observes the actual outlet temperature of EVC. After 38 seconds of blowing, the actual outlet temperature of EVC rises to 410 degrees. It is judged that the ignition is successful, and the blowing continues until the end.
Embodiment 2
[0031] Electrostatic precipitator position: Set the preset outlet temperature of the evaporative cooler to 290°C. In the first 16 seconds before blowing, the water regulating valve of the evaporative cooler is controlled by a fixed opening, and the opening is controlled at 16%. The flow rate of the evaporative cooler 16Nm 3 / h, 16s after the start of blowing, the water distribution regulating valve of the evaporative cooler automatically adjusts the water distribution through the PID control system according to the actual outlet temperature and the preset outlet temperature of the evaporative cooler, and the P and I control parameters are set to 1.0 and 0.8 respectively.
[0032] Converter post: After blowing starts, observe the EVC inlet temperature and actual outlet temperature, and find that the actual EVC outlet temperature rises too fast, and rise to 1000°C within 10s, then judge the EVC outlet temperature detection failure, immediately lift the gun to stop blowing, and no...
Embodiment 3
[0035] Electrostatic precipitator position: Set the preset outlet temperature of the evaporative cooler to 320°C. In the first 16s before blowing, the water regulating valve of the evaporative cooler is controlled by a fixed opening, and the opening is controlled at 15%. The flow rate of the evaporative cooler 15Nm 3 / h, 16s after the start of blowing, the water distribution regulating valve of the evaporative cooler automatically adjusts the water distribution through the PID control system according to the actual outlet temperature and the preset outlet temperature of the evaporative cooler, and the P and I control parameters are set to 1.0 and 0.8 respectively.
[0036] Converter post: After the blowing started, observe the actual outlet temperature of EVC, and found that within 60s, the actual EVC outlet temperature only rose slowly. After 60s of blowing, the actual EVC outlet temperature was only 210°C. It was judged that the ignition failed, and the gun was stopped immedi...
PUM
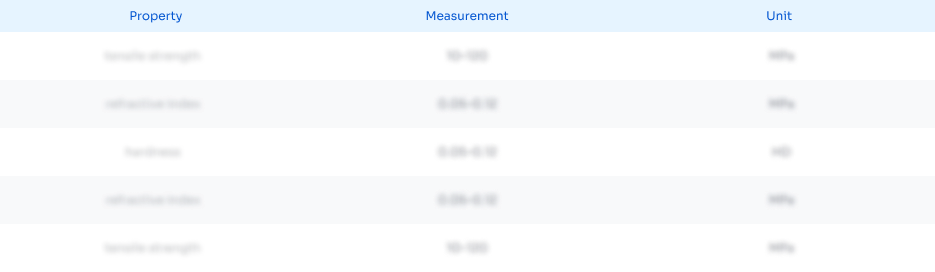
Abstract
Description
Claims
Application Information

- Generate Ideas
- Intellectual Property
- Life Sciences
- Materials
- Tech Scout
- Unparalleled Data Quality
- Higher Quality Content
- 60% Fewer Hallucinations
Browse by: Latest US Patents, China's latest patents, Technical Efficacy Thesaurus, Application Domain, Technology Topic, Popular Technical Reports.
© 2025 PatSnap. All rights reserved.Legal|Privacy policy|Modern Slavery Act Transparency Statement|Sitemap|About US| Contact US: help@patsnap.com