a steelmaking method
A converter blowing and flow technology, which is applied in the manufacture of converters, etc., can solve the problems of explosion venting, reduce the amount of gas recovery, and the electrostatic precipitator is prone to deflagration, so as to prevent explosion venting and reduce damage
- Summary
- Abstract
- Description
- Claims
- Application Information
AI Technical Summary
Problems solved by technology
Method used
Examples
Embodiment Construction
[0013] The steelmaking method of the present invention will be described in detail below in conjunction with examples.
[0014] The steelmaking method according to the present invention includes: within 60 seconds from the start of blowing, the position of the oxygen lance for top-blowing oxygen is controlled to be 1.8m to 2.3m, and the flow rate of oxygen supply is 18000Nm 3 / h~23000Nm 3 / h; within 60 seconds to 90 seconds of blowing, the position of the oxygen lance for controlling top-blown oxygen is 1.5m~1.8m, and the flow rate of oxygen supply is 29000Nm 3 / h~32000Nm 3 / h; after blowing for 90 seconds, the position of the oxygen lance for top blowing oxygen is controlled to be 1.5m~2.6m, and the flow rate of oxygen supply is 40000Nm 3 / h~45000Nm 3 / h; within 11 minutes from the start of blowing, control the flow rate of bottom blowing inert gas to 30Nm 3 / h~50Nm 3 / h; From 11 minutes of blowing to the completion of tapping, control the flow rate of bottom blowing ine...
PUM
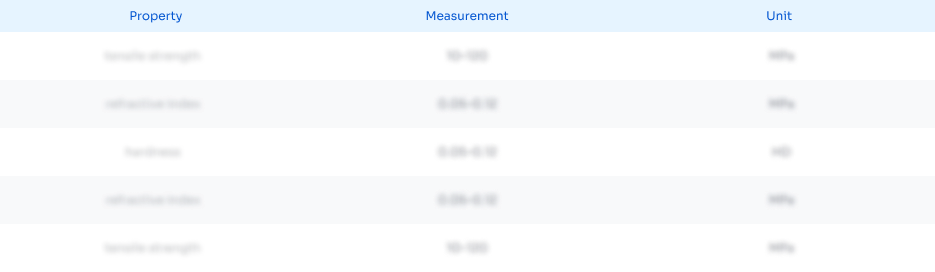
Abstract
Description
Claims
Application Information

- R&D
- Intellectual Property
- Life Sciences
- Materials
- Tech Scout
- Unparalleled Data Quality
- Higher Quality Content
- 60% Fewer Hallucinations
Browse by: Latest US Patents, China's latest patents, Technical Efficacy Thesaurus, Application Domain, Technology Topic, Popular Technical Reports.
© 2025 PatSnap. All rights reserved.Legal|Privacy policy|Modern Slavery Act Transparency Statement|Sitemap|About US| Contact US: help@patsnap.com