Method for preventing vanadium extraction converter dry dedusting system from vented explosion
A converter dry dust removal and dry dust removal technology, applied in the manufacture of converters, etc., can solve the problems of gas explosion venting, undisclosed, vanadium extraction converter dry dust removal system explosion venting, etc., to prolong the service life and save production time Effect
- Summary
- Abstract
- Description
- Claims
- Application Information
AI Technical Summary
Problems solved by technology
Method used
Examples
example 1
[0026] A company’s 200t vanadium extraction converter adopts a dry dedusting system (DDS) to process flue gas (including CO, extremely small dust particles and some metal iron powder), and explosion venting often occurs during use. Use the following method: before mixing iron, confirm the situation in the furnace, start mixing iron when there is no powdery material in the furnace, and at the same time control the speed of the dry dust removal fan to 550rpm; control the iron mixing speed at 90t / min; put the gun after mixing iron Lighting, using low lance position operation, the oxygen lance lance position is controlled between 1.6 ~ 1.8m; 60% of the total coolant consumption (by weight percentage) is added during vanadium extraction and blowing for 45 seconds; when vanadium extraction and blowing for 3 minutes, Add the remaining coolant; when the volume concentration of CO in the flue gas rises to 23%, stop blowing oxygen and raise the gun. After testing, the vanadium extractio...
example 2
[0028] A company’s 200t vanadium extraction converter adopts a dry dedusting system (DDS) to process flue gas (including CO, extremely small dust particles and some metal iron powder), and explosion venting often occurs during use. Use the following method: before mixing iron, confirm the situation in the furnace, start mixing iron when there is no powdery material in the furnace, and at the same time control the speed of the dry dust removal fan to 600rpm; control the iron mixing speed at 50-55t / min; Then lower the lance and fire, adopt low lance position operation, and control the oxygen lance lance position between 1.5-1.6m; add 70% of the total coolant amount (by weight percentage) when vanadium extraction blowing 30s; vanadium extraction blowing At 2 minutes, add the remaining coolant; when the volume concentration of CO in the flue gas rises to 23%, stop blowing oxygen and raise the gun. After testing, the vanadium extraction converter dry dust removal system in this exa...
PUM
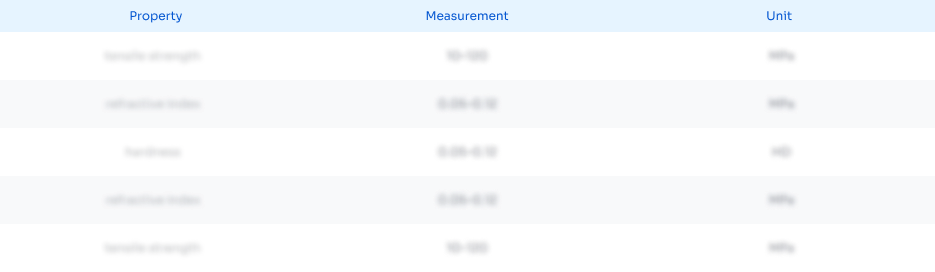
Abstract
Description
Claims
Application Information

- R&D
- Intellectual Property
- Life Sciences
- Materials
- Tech Scout
- Unparalleled Data Quality
- Higher Quality Content
- 60% Fewer Hallucinations
Browse by: Latest US Patents, China's latest patents, Technical Efficacy Thesaurus, Application Domain, Technology Topic, Popular Technical Reports.
© 2025 PatSnap. All rights reserved.Legal|Privacy policy|Modern Slavery Act Transparency Statement|Sitemap|About US| Contact US: help@patsnap.com