Optical proximity correction method and manufacturing method of mask
A technology for optical proximity correction and reticle, which is applied in optics, originals for opto-mechanical processing, and photo-engraving processes on pattern surfaces, which can solve the problems of low accuracy of optical proximity correction and achieve high precision.
- Summary
- Abstract
- Description
- Claims
- Application Information
AI Technical Summary
Problems solved by technology
Method used
Image
Examples
Embodiment Construction
[0028] As mentioned in the background, the existing optical proximity correction method has poor accuracy.
[0029]An optical proximity correction method, comprising: providing a target etching pattern, the target etching pattern including a plurality of sub-target etching patterns; obtaining a mask layer pattern corresponding to the sub-target etching pattern according to an etching offset table; The OPC correction is performed on the film layer graphics to obtain the corrected graphics.
[0030] A mask is made with the corrected pattern, and actual exposure is performed on the mask to obtain an actual exposure pattern, and there is a certain positional deviation between the actual exposure pattern and the previous layer pattern. The above positional deviation is usually caused by the thermal expansion of the target etching pattern during the process and the positional deviation of the mask. However, the process of performing OPC correction on the pattern of the mask layer d...
PUM
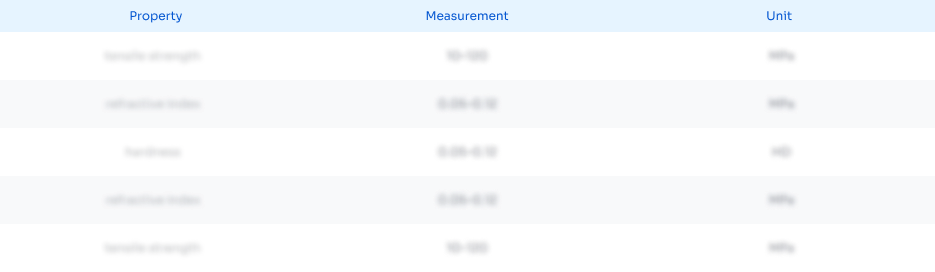
Abstract
Description
Claims
Application Information

- Generate Ideas
- Intellectual Property
- Life Sciences
- Materials
- Tech Scout
- Unparalleled Data Quality
- Higher Quality Content
- 60% Fewer Hallucinations
Browse by: Latest US Patents, China's latest patents, Technical Efficacy Thesaurus, Application Domain, Technology Topic, Popular Technical Reports.
© 2025 PatSnap. All rights reserved.Legal|Privacy policy|Modern Slavery Act Transparency Statement|Sitemap|About US| Contact US: help@patsnap.com