Production process of tencel wool blended yarn
A production process and blended yarn technology, which is applied in yarn, textiles and papermaking, etc., can solve the problems of high initial dyeing rate, color difference, left and right color difference, etc., and achieve the effect of beautiful fabric luster, wearing performance, and smooth and comfortable hand feeling
- Summary
- Abstract
- Description
- Claims
- Application Information
AI Technical Summary
Problems solved by technology
Method used
Examples
Embodiment 1
[0014] A kind of Tencel wool blended yarn production process is characterized in that, described production process comprises the following steps:
[0015] Step 1: Select Tencel fiber and Merino wool with a blending ratio of 70%:30%. The Tencel fiber specification is: 1.4dtex Tencel fiber, and the Merino wool specification is: 17.2mic Merino wool;
[0016] Step 2: After blending, first needle combing, second needle combing, third needle combing, and four needle carding processes, the tencel fiber and merino wool are combined and then drafted to form a roving sliver, and the roving sliver is carded. Make the roving sliver as straight as possible, and the final needle speed is 180m / min, which is conducive to making the sliver evenly mixed and reducing magazines;
[0017] Step 3: The use of shot-medium hard rubber rollers is beneficial to strengthen the control of floating fibers, reduce the twisting triangle area, and improve the yarn quality. The new compact spinning technology...
Embodiment 2
[0020] A kind of Tencel wool blended yarn production process is characterized in that, described production process comprises the following steps:
[0021] Step 1: Select Tencel fiber and Merino wool with a blending ratio of 70%:30%. The Tencel fiber specification is: 1.4dtex Tencel fiber, and the Merino wool specification is: 17.2mic Merino wool;
[0022] Step 2: After blending, first needle combing, second needle combing, third needle combing, and four needle carding processes, the tencel fiber and merino wool are combined and then drafted to form a roving sliver, and the roving sliver is carded. Make the roving as straight as possible, and the final needle speed is 200m / min;
[0023] Step 3: Use shot-medium-hard rubber rollers, which is beneficial to strengthen the control of floating fibers, reduce the twisting triangle area, and improve the quality of yarn;
[0024] Step 4: Steam the yarn three times, after 0.5 hour treatment at 60°C, place it in vacuum for 30 minutes; a...
PUM
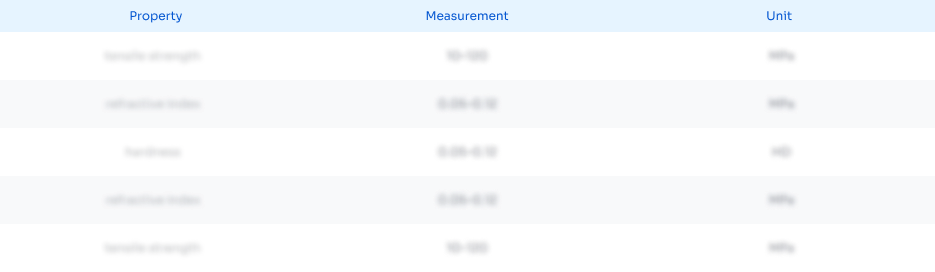
Abstract
Description
Claims
Application Information

- R&D Engineer
- R&D Manager
- IP Professional
- Industry Leading Data Capabilities
- Powerful AI technology
- Patent DNA Extraction
Browse by: Latest US Patents, China's latest patents, Technical Efficacy Thesaurus, Application Domain, Technology Topic, Popular Technical Reports.
© 2024 PatSnap. All rights reserved.Legal|Privacy policy|Modern Slavery Act Transparency Statement|Sitemap|About US| Contact US: help@patsnap.com