A composite high-efficiency and precise dressing method for superabrasive grinding wheels
A superhard abrasive and composite technology, which is applied in the direction of abrasive surface adjustment devices, grinding/polishing equipment, grinding machine parts, etc., can solve problems such as complex process, low dressing accuracy, and adverse effects of grinding wheel dressing accuracy
- Summary
- Abstract
- Description
- Claims
- Application Information
AI Technical Summary
Problems solved by technology
Method used
Image
Examples
Embodiment Construction
[0038] The technical solutions of the present invention will be described in further detail below through specific implementation methods.
[0039] Such as Figure 1-Figure 6 As shown, a superabrasive grinding wheel composite efficient precision dressing method comprises the following steps:
[0040] Step 1. Abrasive Waterjet Rough Repair:
[0041] The superabrasive grinding wheel rotates at a certain speed, and the injection direction of the abrasive water jet 3 is perpendicular to the axis of the superabrasive grinding wheel 1, and forms a certain angle with the tangent line of the outer circle of the superabrasive grinding wheel 1. The tangent line of the outer circle is consistent, and the spraying effect is small. If the angle is too large, it is easy to remove too much bonding agent and abrasive particles. Therefore, the angle should be controlled within a reasonable small angle range;
[0042] At the same time, the abrasive water jet nozzle 2 reciprocates along the cr...
PUM
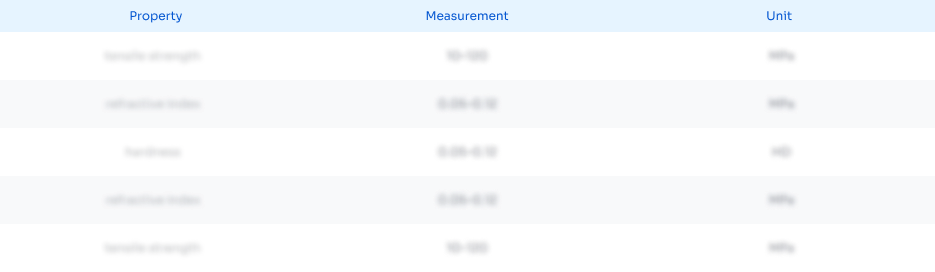
Abstract
Description
Claims
Application Information

- R&D
- Intellectual Property
- Life Sciences
- Materials
- Tech Scout
- Unparalleled Data Quality
- Higher Quality Content
- 60% Fewer Hallucinations
Browse by: Latest US Patents, China's latest patents, Technical Efficacy Thesaurus, Application Domain, Technology Topic, Popular Technical Reports.
© 2025 PatSnap. All rights reserved.Legal|Privacy policy|Modern Slavery Act Transparency Statement|Sitemap|About US| Contact US: help@patsnap.com