Preparation method of natural latex pillow product
A technology of natural latex and pillow cushion, which is applied in the field of low-temperature process preparation of natural latex pillow cushion products, can solve the problems of high viscosity, easy blockage of foaming machines and equipment transmission pipes, etc., to avoid particle agglomeration, reduce cleaning and maintenance and The effect of maintenance workload and shortened production cycle
- Summary
- Abstract
- Description
- Claims
- Application Information
AI Technical Summary
Problems solved by technology
Method used
Examples
Embodiment 1
[0032] (1) Take 100 parts of centrifugally concentrated natural rubber latex, adjust the ammonia content to 0.22% at a temperature of 16°C and ventilation conditions, and obtain Latex A;
[0033] (2) Add latex A to the aging tank, and add foaming agent (a mixture of potassium vegetable oleate and potassium ricinoleate at a mass ratio of 5:1) while stirring at 50rpm, 4 parts of vulcanizing agent (sulfur) 2 parts, 1 part of anti-aging agent (anti-aging agent WL), 1.8 parts of vulcanization accelerator (zinc 2-mercaptobenzothiazole), and aging at 20°C for 8 hours after the addition of materials, to obtain latex B;
[0034] (3) Add latex B to the foaming machine for foaming, and control the temperature of the material at 20°C during foaming, and then add a gelling agent (the mass ratio of sodium fluorosilicate to potassium chloride is 3: 1 mixture) 1 part, active agent (zinc oxide) 3 parts and vulcanization accelerator (di-o-toluene guanidine) 0.9 parts (the active agent and vulca...
Embodiment 2
[0039] (1) Take 100 parts of centrifugally concentrated natural rubber latex, adjust the ammonia content to 0.20% at a temperature of 20°C and ventilation conditions, and obtain Latex A;
[0040] (2) Add latex A to the aging tank, and add foaming agent (a mixture of potassium vegetable oleate and potassium ricinoleate at a mass ratio of 3:1) while stirring at 35 rpm, 3 parts of vulcanizing agent (sulfur) 1.5 parts, 0.8 parts of anti-aging agent (anti-aging agent WL), 1.0 parts of vulcanization accelerator (zinc 2-mercaptobenzothiazole) and 0.9 parts of vulcanization accelerator (zinc diethyldithiocarbamate), after the addition is completed Latex B was obtained by aging at 18°C for 12 hours;
[0041](3) Add latex B to the foaming machine for foaming, and control the temperature of the material at 20°C during foaming, and then add a gelling agent (the mass ratio of sodium fluorosilicate to potassium chloride is 2: 1 mixture) 2.7 parts, active agent (triethanolamine) 4 parts a...
Embodiment 3
[0046] (1) Take 100 parts of centrifugally concentrated natural rubber latex, adjust the ammonia content to 0.17% at a temperature of 18°C and ventilation conditions, and obtain Latex A;
[0047] (2) Add latex A to the aging tank, and add foaming agent (a mixture of potassium vegetable oleate and potassium ricinoleate at a mass ratio of 7:1) while stirring at 40rpm, 1.5 parts of vulcanizing agent 4,4 '-dithiodimorpholine) 2.1 parts, anti-aging agent (anti-aging agent WL) 1.2 parts, vulcanization accelerator (2-thiol benzothiazole) 0.8 parts and vulcanization accelerator (2-thiol benzothiazole Zinc) 1.0 parts, aging at 27°C for 5 hours after the addition of materials, to obtain latex B;
[0048] (3) Add latex B to the foaming machine for foaming, and control the temperature of the material at 20°C during foaming, and then add a gelling agent (the mass ratio of sodium fluorosilicate to potassium chloride is 5: 1) 1.9 parts, active agent (zinc stearate) 3.5 parts and vulcaniza...
PUM
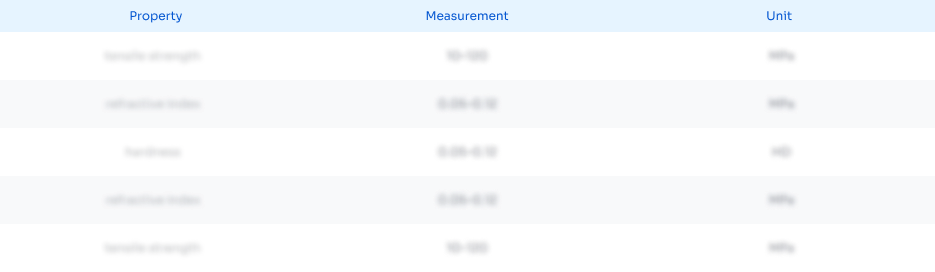
Abstract
Description
Claims
Application Information

- R&D Engineer
- R&D Manager
- IP Professional
- Industry Leading Data Capabilities
- Powerful AI technology
- Patent DNA Extraction
Browse by: Latest US Patents, China's latest patents, Technical Efficacy Thesaurus, Application Domain, Technology Topic, Popular Technical Reports.
© 2024 PatSnap. All rights reserved.Legal|Privacy policy|Modern Slavery Act Transparency Statement|Sitemap|About US| Contact US: help@patsnap.com